Imagine a factory where the digital twin of every machine and product allows you to simulate and optimize production processes even before they are implemented in the real world. This is the industrial metaverse. The industrial metaverse represents a revolutionary concept that bridges the physical world of manufacturing with a digital environment. Essentially, it is an extended virtual reality that enables the creation of digital twins for physical factories, machines, and products. This allows companies to optimize production processes, accelerate the development of new products, and enhance collaboration between various teams and robots.
At MSV 2024, we will demonstrate its potential using a robotic cell for autonomous manipulation, equipped with a KUKA robot capable of executing precise pick-and-place operations autonomously. These operations are controlled by advanced 6D pose estimation techniques using computer vision methods. The entire cell is fully virtualized in Siemens’ Tecnomatix Process Simulate, which is integrated with Nvidia Omniverse.
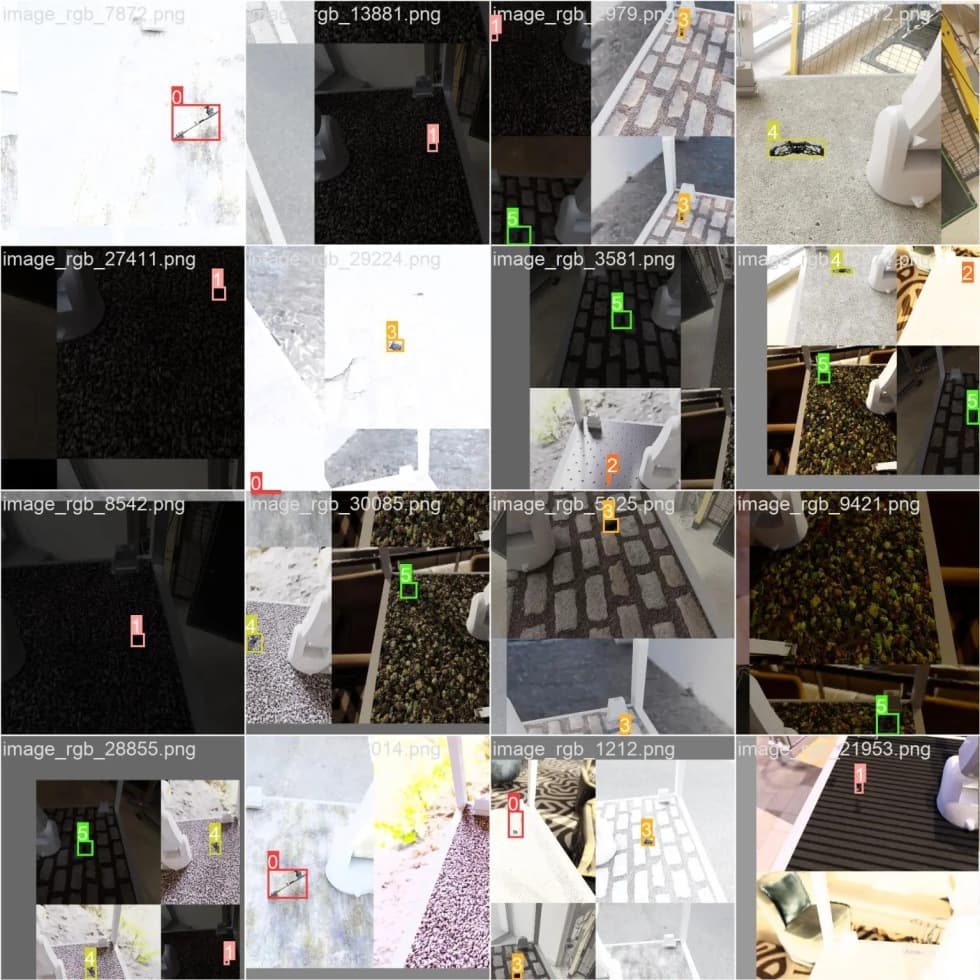
This environment, leveraging randomization and advanced simulation capabilities, allows for the training of AI models for object recognition and manipulation. Additionally, the cell is equipped with technology for the automated generation of custom end-effectors, manufactured via 3D printing technologies. The entire cell is also accessible in virtual reality.
The robotic cell integrates a physical KUKA robotic arm equipped with industrial cameras for computer vision. These cameras utilize the 6D MegaPose algorithm for real-time spatial orientation and object position estimation.
A digital twin hosted on the NVIDIA Omniverse platform (alongside Process Simulate virtualization software and KUKA.OfficeLite) mirrors the physical cell in real time. This enables the creation of synthetic datasets for training machine learning models, offering high flexibility when combined with tools for end-effector design. The modular design and unified interface ensure scalability for seamless transition to more complex manufacturing systems.
What makes this technology unique?
The uniqueness of this technology lies in its ability to accurately simulate and test robotic cells in a virtual environment, significantly reducing development time and increasing efficiency. By integrating with the NVIDIA Omniverse platform and leveraging synthetically generated datasets for machine learning model training, we achieve high accuracy and fidelity in simulations, which are reflected in physical environments.
This technology stands out for its seamless integration of a physical robotic cell with a highly precise digital twin. This combination enables real-time simulation, monitoring, and optimization, as well as feasibility studies. The ability to autonomously generate and adapt end-effectors for any object, combined with advanced 6D pose estimation, makes this a universal and adaptive solution for complex manipulation tasks.
How can this technology be applied in practice?
The technology can be utilized at various stages of the manufacturing process, from design and testing to final deployment and production optimization. Using a digital twin, it is possible to simulate and test new production processes without the need for physical prototypes, saving both time and costs.
The solution can minimize manual interventions and increase production efficiency. The digital twin enables pre-production simulation, reducing downtime and errors in real-world applications. It also facilitates rapid adaptation to new tasks or production lines by reconfiguring the virtual model instead of physical equipment. A key advantage is the simulation of camera systems and the ability to generate end-effectors.
What are the results or benefits for users?
The primary benefits for users include reduced development time, lower prototype costs, and increased production accuracy and efficiency. Our solution also enables faster and easier adjustments and optimizations of production processes thanks to realistic simulations in the virtual environment.
How can this technology help businesses?
By enabling the simulation and optimization of production processes in a virtual environment, the technology significantly reduces costs and enhances manufacturing efficiency. It can benefit industries such as engineering, automotive, electronics, and other manufacturing sectors requiring high levels of automation and adaptability.
What inspired us to develop this technology? How long did development take? What were the key milestones?
The growing need for adaptable, autonomous systems in modern manufacturing inspired this technology. As production lines become more complex and the demand for customization increases, it became evident that a solution offering flexibility without compromising precision or efficiency was necessary. The development process, which took over two years, was driven by milestones achieved through the progressive integration of the NVIDIA Omniverse platform.