English translation of the original article by Jan Prokeš, published in Czech newspaper Hospodářské noviny (Economic Newspaper), 3 May 2024
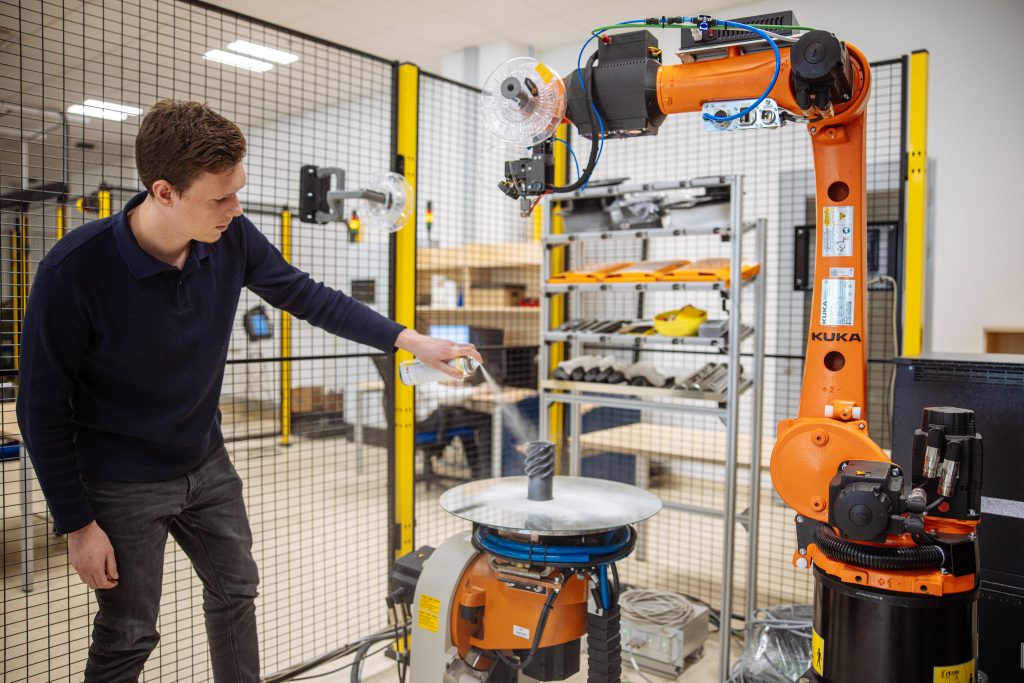
During his studies at the Faculty of Mechanical Engineering of the Czech Technical University, Tomáš Jochman was looking for a part-time job. He finally succeeded at the Czech Institute of Informatics, Robotics and Cybernetics (CIIRC), which is part of his university. Today, Jochman has been working there for five years and is involved in the development of Industry 4.0 technologies that make life easier for businesses in various fields. “I started with research on the robotic bar, which was then in a pilot version and we were trying to take it further. I combined the project with my thesis at the time,” he recalls. He is currently working on robotic 3D printing, for example.
Printing large parts using robots is just one of the things Jochman and his 30 or so colleagues at the RICAIP Testbed Prague at CIIRC are working on. They help companies that decide to go digital to find solutions that are right for them and push their production forward through innovation. “We offer consultations, feasibility studies or testing of technologies before a company decides to invest in them in its factory,” says Testbed director Pavel Burget. “Our big advantage is our infrastructure. At testbed, we have machines, robots, camera systems or 3D printers that are the same as those commonly used in industry,” he adds.
Czech Institute of Informatics, Robotics and Cybernetics
CIIRC scientists work with large companies such as Škoda Auto, Lego, Continental and T-Mobile. “A lot of our manufacturing clients are undergoing a transformation to the digital world, but it is extremely costly. It is therefore important for them to have a partner who understands the issues and can show them how technology works in a real environment,” explains Jakub Kopecký from T-Mobile.
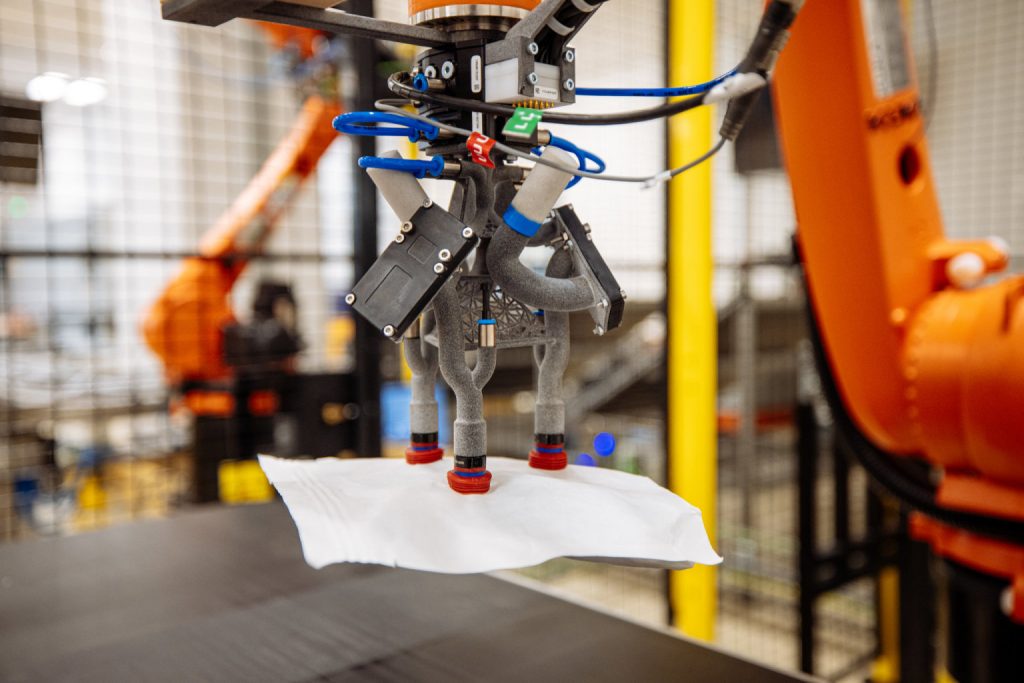
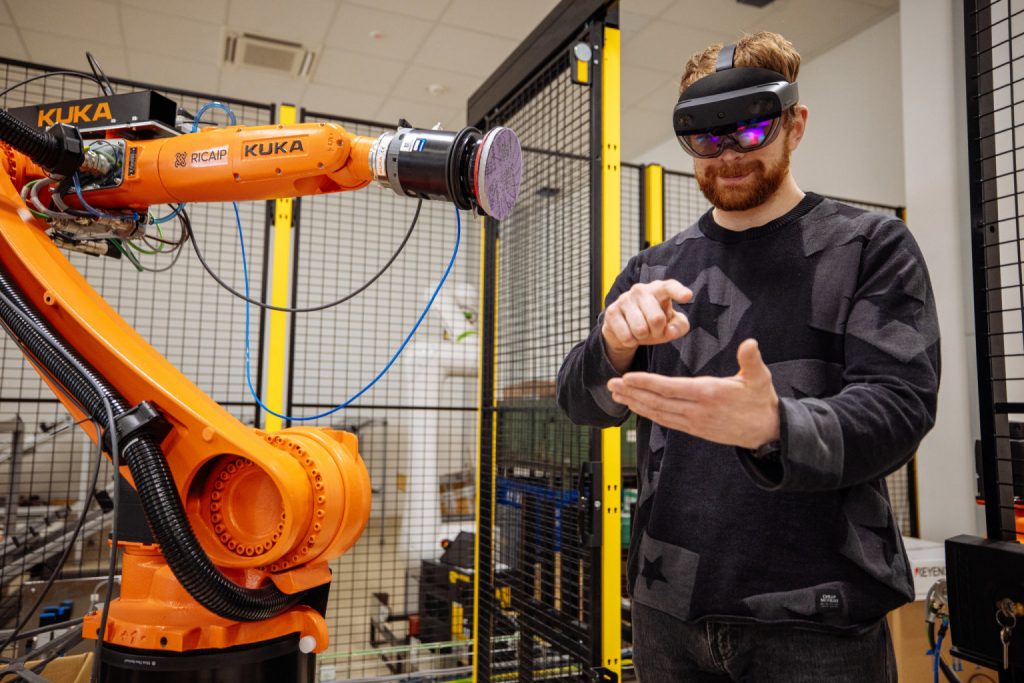
In the testbed at the CIIRC, companies can test how the new technology they are considering really works and whether it is worth investing in a change of production. “For example, we had a client who manufactures in steel but wanted to switch to a different type of production and also material. Rather than buy a huge 3D printing machine for a lot of money, he can try everything out here,” says Kopecký.
Three years ago, operator T-Mobile installed the first private campus 5G SA network in the Czech Republic in the local testbed to design and test various scenarios that show commercial entities how 5G networks can help them with production innovation. One example of a successful project in the RICAIP Testbed is the development of a device for the so-called 5G IoT Gateway, which transmits data from various sensor modules over the 5G network. In addition, this is a project whose results have already been commercialised by the CIIRC – a spin-off company, Trix Connections, has been set up within the CTU to manufacture the sensors and supply them to T-Mobile.
In many companies, this wireless network is replacing conventional wired infrastructure. “It’s scalable anywhere and companies don’t have to invest a lot of money in cabling. It looks simple, but after covid, manufacturing has changed a lot, so the importance of wireless has grown. Companies used to make one product on the lines for a year, for example, and now they often change production three times a week,” says Kopecký.
The scenario of frequent reconfiguration of production corresponds to another example that was implemented in RICAIP Testbed. This is a production line in which each robot is a separate cell that can be separated and moved elsewhere at any time. The communication of the cells is ensured by a 5G SA connection (implemented via the 5G IoT Gateway developed), which, in addition to transmitting images from the cameras, also transmits control and safety signals using the industrial protocols Profinet and Profisafe. “Each cell has a defined set of functions it is capable of performing. The order in which the operations are performed is determined by the master production management system, the MES. The advantage is that if I want to change something in production, I don’t have to reprogram the robots immediately, I just change the assignment for the MES,” says Burget.
This type of scenario is based on the advantages of 5G wireless network, which are mainly guaranteed latency level, industrial robustness including security and the possibility to configure the service for the needs of a specific application.
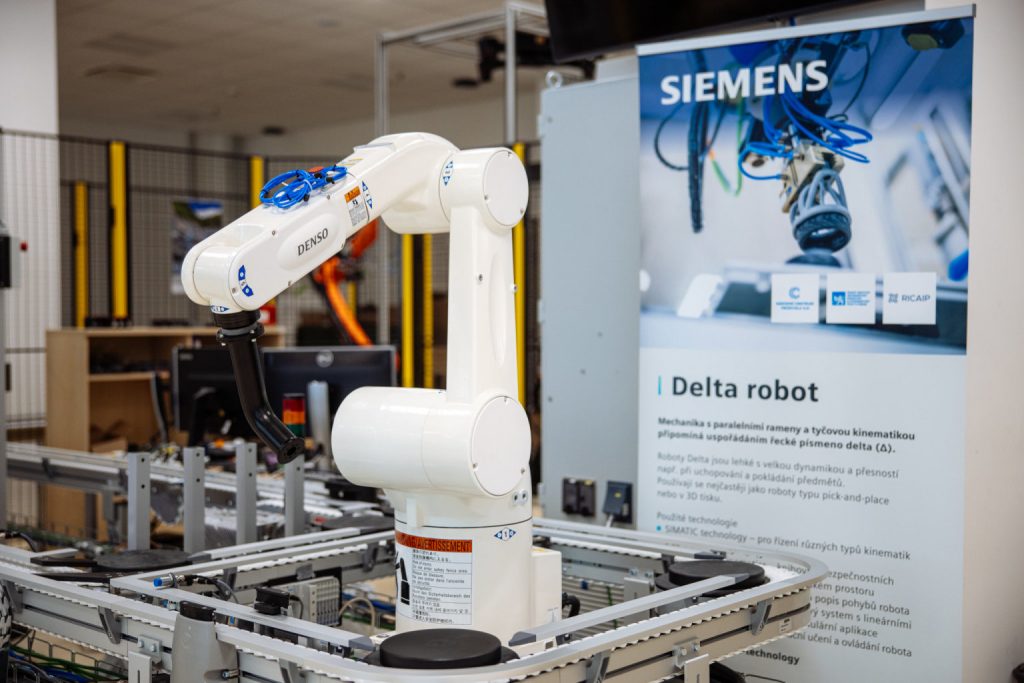
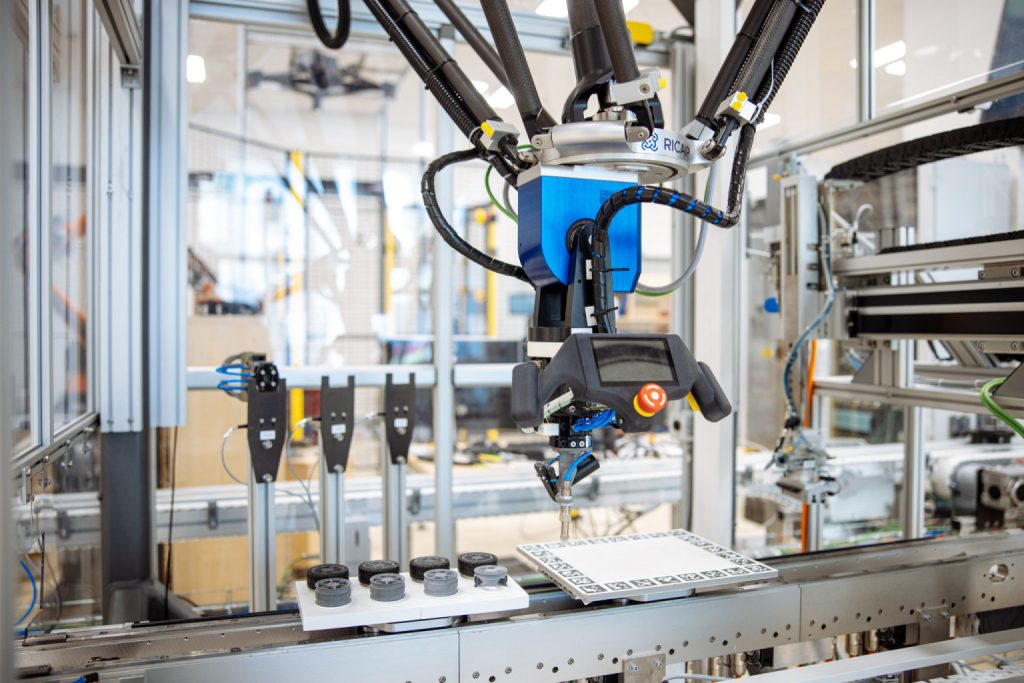
The CIIRC also works on a market-based basis with other companies that contact the institute, for example, to request a consultation. But for smaller companies, there is now a way to access know-how at a significant discount, which in most cases is as much as 100 percent. Currently, programmes financed by EU funds are being launched, in which the CIIRC is also involved. These are the European Digital Innovation Hubs (EDIH) and AI-Matters networks, in which tens of millions of euros are available for entrepreneurs. “The aim of these projects is to help companies kick-start innovation,” says Burget. “EDIH has been running since the end of last year and AI-Matters is just now getting underway. In both programmes, we have already launched several concrete projects for companies that want to use them. We are trying to encourage companies not to be afraid and to want to innovate. A discount of up to 100 percent can overcome their initial uncertainty about whether innovation is even worth tackling and investing in,” he adds.
According to Kopecký from T-Mobil, the digital transformation in the country is about one-third complete and its need will become more and more massive. He sees the greatest demand for investment in Industry 4.0 in large companies that have sufficient capital. However, it also works relatively well for smaller companies with up to 50 employees, where the speed of decision-making on innovation is very high. “Demand is so far greatest from industry, but other interesting sectors such as media or healthcare organisations are also joining in,” says Kopecký.
Photos: Lukáš Bíba, HN
