Author: Darja Thomasová, Hospodářské noviny
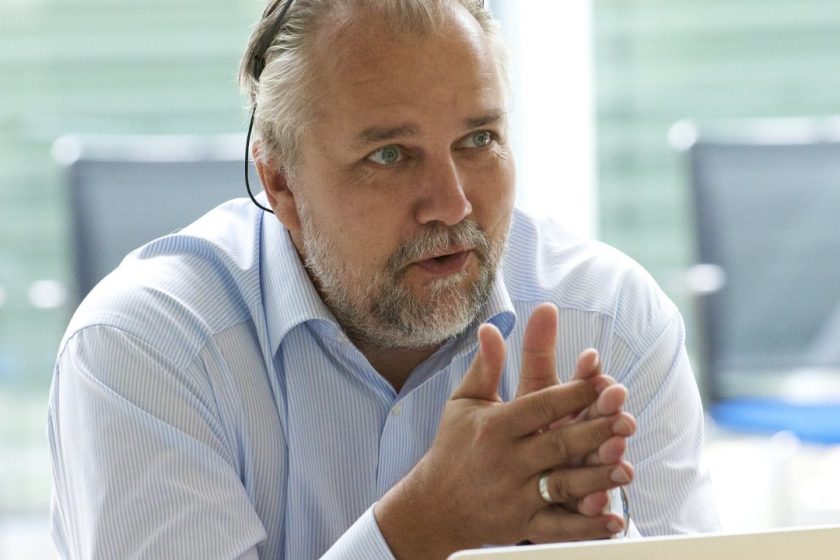
Ten years ago, visions of the Fourth Industrial Revolution, also known as Industry 4.0, were formulated. Today, it is clear that mass customization is not developing so fast and it is necessary to work to increase the quality of production with an emphasis on zero scrap, not only due to climate change. New jobs are being created, robot mobility is increasing, and artificial intelligence can even retrain employees. Tilman Becker, a German scientist in the field of artificial intelligence and director of the Czech RICAIP centre focused on research in the field of Industry 4.0, presents the current results and long-term prospects.
In January last year, you became the head of the Research and Innovation Center for Advanced Industrial Production RICAIP at the Czech Institute of Informatics, Robotics, and Cybernetics CTU in Prague (CIIRC CTU), which opened in September 2019. It is an innovative and strategic project in the Czech Republic. German cooperation. How do you feel after almost two years as a director?
Very sure. It is a major project, as you mentioned. We have a lot of activities up and running, we are building testbeds and we have big plans for the future. Although in the beginning, it may seem that the progress is not significant, we have done a great deal of work to date. We are even able to show some results, as was the case during the August visit of German President Frank-Walter Steinmeier. During less than an hour spent in the testbed for Industry 4.0 at CIIRC CTU in Prague, we were able to present several experiments to him.
Which specifically?
Several robots, including those that can work with humans. In testbeds in Brno and Prague, we have a number of production lines and machines, autonomous robots and other equipment. We test production technologies, including machining on large machines, which combine 3D printing with milling. This makes it possible to produce very diverse components automatically.
RICAIP received support from the European Commission in the amount of almost 50 million euros, ie 1.2 billion crowns. Is this a sufficient amount for research in such a progressive field?
Yes and no. Definitely enough to start. It is an investment that is expected to return in the form of subsequent sustainability of the RICAIP research centre. Of course, this will no longer be financed from this amount, but through other new projects. That is why we actively try to work with public finances and also cooperate with industry and obtain money from specific partners to finance specific tasks.
One of the goals of the project is to connect the testbeds associated in RICAIP with other research institutes and move them to the world level. Who do you think is the absolute leader in the field of robotics and cybernetics?
There is no absolute leader in this field. In each country, we work in a specific segment and the individual results are astounding. It is worth mentioning, for example, the Netherlands. It is a relatively small state, but it is very active in matters of Industry 4.0. In Europe, we work with a number of partners from different countries. These include, of course, Germany, as well as France, Spain and Denmark, and we are still open to further cooperation.
How is Czechia in particular?
The Czechia is one of the eastern countries that is making the most progress. Of course, one of the reasons is the education system in the field, which is at the highest level. And also historically, this country is very much connected with industrial production. You can also see this in the example of the Škoda Auto company, which is sometimes more successful in terms of a product than the parent Volkswagen. The domestic government is very open in terms of investing in advanced technologies, which ensures a good position of the Czech Republic in the field of research Industry 4.0. The financial contribution is important because it is a means that is also a long-term investment, and it will pay off in the end. And thanks to the fact that the expertise is located within the state, the Czechia can manage the development in the field rather than if it is foreign investments, foreign factories or research that is carried out in other countries.
The Czech Minister of Industry and Trade Karel Havlíček is convinced that RICAIP will provide significant support to small and medium-sized companies. What fields does it primarily concern?
At RICAIP, we have focused from the beginning mainly on the manufacturing and processing industries. We are interested in production and assembly or a combination of different technologies, such as machining, robotic manipulation and additive production. In some areas, however, we also overlap with, for example, healthcare, research for the construction industry or the chemical and pharmaceutical industries.
How long is the journey from the beginning of the research to the application of specific results in production?
It really depends on the complexity of the project. On the steps to be taken. And also whether the specific equipment is already physically located in the company, or it is necessary to assemble a completely new production line. If the machine is already in place and it is about creating a software solution, it can only take a few weeks. But if a new production line needs to be built, such a project will take several years.
Do you address companies with the results of your research, or do you meet with interest from them?
Fortunately, this is a two-way process. One of our tasks is to provide the results of our work and research and also to recognize the needs of the industry together with the industry. RICAIP is linked to many initiatives, such as digital innovation centres or the National Industry Center 4.0. And it is through similar platforms that we actively communicate with the industry about what it needs and what we are developing and researching. But of course, there are more conservative companies that are holding back, and also companies that are very innovative and actively contact us.
Can you list specific companies?
These are really big players in the Czech Republic. For example, we work closely with Škoda Auto. Important partners are Siemens or T-Mobile, which also provide technology. Lego in the Czech Republic also manufactures and solves other complex tasks such as packaging and transport. However, we are also open to cooperation with smaller companies and we also support spin-off companies, ie those that were founded by students, collaborators and researchers. Examples are TRIX Connections, Pocket Virtuality or Factorio Solutions.
What is holding back progress in smaller companies?
Sometimes SMEs are trapped in their success, producing something for decades, they have the know-how, but they forget to notice that the market can change. The current product may not be successful in the future and they need to adapt to market developments, preferably early and creatively. And I think the most difficult task is to establish a vision of what products and services may look like in the future.
Which fields will not do without a high degree of automation in such ten years?
Certainly, these are and will continue to be the sectors using pure automation, in which robots perform mass production and serve to eliminate hard work, or it is, for example, a dangerous environment. And also the fields that deal with mass production, however, offer the diversity that the end customer requires in the form of an individualized product. Such companies need complex robotic systems and also use them widely today. In general, this is any area where the use of mass customization blends with the market, which can benefit from it.
For example?
The automotive industry is a perfect example. Even if you know in advance which model you want to buy, let’s say the Škoda Octavia, you have a million options to choose from: different colours, equipment, engines, gearboxes and the like. But even such a range of possibilities may not be enough in the future and maybe much more individualized using robots.
The basic visions of digitization and complex automation of production appeared ten years ago and were named the Fourth Industrial Revolution or Industry 4.0, how are they being fulfilled?
It is not a phenomenon that has occurred from day to day and has changed everything. However, it is justified to call this development given the fast. Over the last few years, we have observed significant changes in the construction of new production lines, but also where there has been an improvement of existing machines or the integration of older machines into current processes. Investment in production only makes sense if the production machine will be used for years, in some cases decades. The goal is not to throw away an older machine and invest again without a return. We have also addressed a number of initial challenges in terms of interconnecting machines and collecting available data, which we can analyze and benefit from today.
Have key visions changed over the years, and how do they affect developments so far?
Yes. Here I would mention the initial vision of complete customization. It is still justified, but it is far more difficult to achieve and is not implemented as quickly as expected. And not every area can benefit from it, and it may not be as important as originally thought. Yes, it’s great to be able to design completely individual sneakers and watch how the robot assembles it for you in the store, but it’s definitely not what the market really needs.
One more thing?
After those ten years, the issue of climate change and whether we can achieve more energy-efficient production is also very important. Digitization can help with that. In the coming years, for example, we will struggle to increase the quality of production, including efforts to achieve zero production errors, which will reduce resource waste. We believe that this will be possible also thanks to the implementation of the methodology developed within Industry 4.0.
What discovery over the past decade do you consider to be absolutely groundbreaking?
The most groundbreaking discoveries concern machine learning, one of the key technologies within Industry 4.0. Real-time object recognition in video is something that is very easy to achieve today. As for robotics, it develops in the field of mobility, ie the movement of machines, or autonomous control. Both areas work quite well together. We also have a better understanding of how to take all the digital data that is increasingly available and integrate it at the factory level. RICAIP takes this a step further to the level of integration between factories. It is no longer just about reference theoretical models, but real implementations in large companies, which Siemens, for example, carries out with its MindSphere product.
Can you name the most common problems in implementing digitization in companies?
One of the biggest problems is the modernization of existing production machines. This may consist in their retrofitting with digital technologies and components, such as additional sensors, which will enable better automatic control of their operation and thus be involved in the overall digitization of the production process. Then also the correct identification of the area where digitization is most helpful and profitable, where it makes the most sense in the functioning of the company. Last but not least, there is the issue of security and data protection – very important, but sometimes neglected.
What are the most common cybersecurity questions in your community?
In many ways exactly the same as in other spheres. I do not see much difference in the handling of data in the production environment and, for example, insurance companies. Having a firewall throughout the factory is very important, but again very similar to having a secured firewall, for example in a publishing house. But we live in the real world, and the impact of physical security is very different. When a computer at a bank stops working, it’s annoying to clients, but it doesn’t necessarily hurt anyone right away. However, if the robot does something unusual and suddenly starts moving differently, there is a risk of injury to people in production, and that is a problem. Physical security and its connection with cybersecurity is a challenging task.
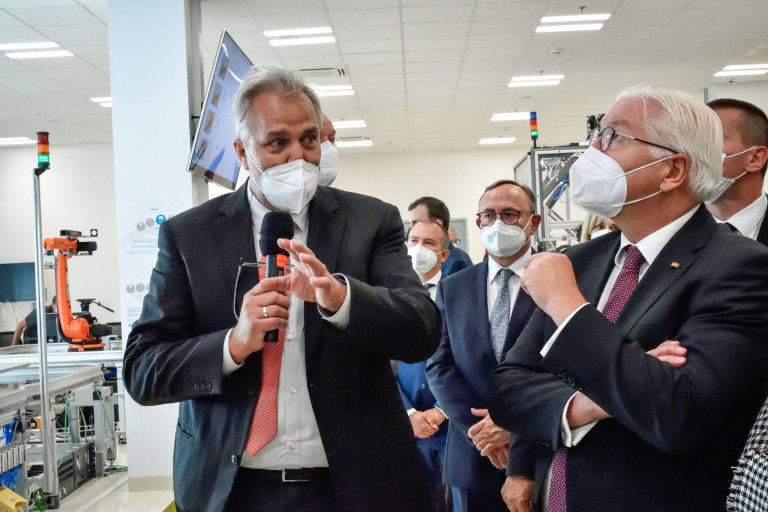
Prior to joining RICAIP, you worked for almost 25 years at the German Research Center for Artificial Intelligence (DFKI). Was the new position a logical step in your career?
Not necessarily. The whole project started in 2016, when the first framework cooperation began, initiated by the German professor and researcher in the field of artificial intelligence Wolfgang Wahlster and also the founder and scientific director of CIIRC CTU in Prague, Professor Vladimír Mařík. At that time, an agreement on scientific cooperation was signed in the presence of German Chancellor Angela Merkel, which actually started the project. I have been a part of it from the very beginning, so it may seem that in my case it was a logical step. But since I worked for DFKI for more than 20 years at the time, I had no plans to leave. But I’m very happy that I applied for the position of director and eventually filled her.
What was it like to leave DFKI after such a time?
It gives you a whole new perspective on your previous work. I’ve been doing research all my life, and today, even though I’m trying to keep up, it’s a little harder to get involved in research because I handle a lot of managerial tasks. But I still work very intensively with DFKI, it’s not like I’m leaving completely. Today I am in charge of a very specific task, as the management of the RICAIP centre involves working directly for the four institutions that are partners and support the project. In addition to DFKI and CIIRC CTU, there are also the Central European Institute of Technology of the Brno University of Technology (CEITEC BUT) and the German Center for Mechatronics and Automation Technology ZeMA.
How do you remember working with one of the fathers of the Fourth Industrial Revolution, Wolfgang Wahlster, what you learned from him?
Be sure to keep up with what’s going on in the world. And one of the main things I’ve learned is to always take an extra step to make everything perfect. And also the fact that even in the highest positions there are only people who work hard, so the level in the profession is accessible to everyone. It is always a combination of talent and hard work.
The use of cyber-physical systems has certain advantages, but at the same time, as in the case of previous industrial revolutions, it is displacing existing employees who will have to look for a new job. Do they have a chance to retrain in the field?
Definitely yes! One of the specifics of current assistive technologies is that they communicate with a person at various levels, including learning systems. Five years ago, one partner at DFKI and I developed a system that helped students and temporary workers with zero knowledge of assembly procedures assemble electric motors. There were 200 variations of this engine, but thanks to the pictures, videos, spoken interaction, including the emphasis on safety measures, everything worked great. Many existing job positions may change within the company, but employees can be retrained.
But we are still talking about one employee in a place where there could have been ten before…
Yes, part of the vision of Industry 4.0 is focused on production productivity. And some people are free to do other work, and we need to find tasks that they can do. From the experience of previous industrial revolutions, we can learn how to deal with it properly. It is important to gradually be aware of the coming changes, to address them at the societal level and to acquaint politicians with the prospects.
In Germany, similar changes occur a little earlier, what is the experience?
Finding an employee is more of a challenge than solving the problem of people losing their jobs. At present, a person with different levels of qualification has no problem finding employment in Germany. New positions are also constantly opening up. The qualification itself can be very much supported by technology. The education systems I mentioned provide experience and deepen skills. In the case of certain machines, it is not even necessary to study for years, it is enough to complete a two-week course, where, in cooperation with the machine, one learns everything necessary. It will be similar in the Czech Republic.
What new occupations could arise in connection with the impacts of Industry 4.0?
Some professions are built on existing ones. But they have changed so much that they suddenly need to be renamed. For example, working with data, data analysts. It is a new job name that already has a history. They are people who work in statistics, are engaged in economic theory, mathematics. Other new professions will emerge in a similar way. It is also important to transform the work of employees in factories thanks to completely new tools. It moves from heavy manual work to the supervision and control of robots and systems. It paves the way for more creativity and the discovery of new ways to work faster and cheaper.
These days, several European artists are learning about artificial intelligence and machine learning as part of the Goethe-Institut’s residency program at the RICAIP Center. What does the dialogue between art and artificial intelligence look like?
From the interaction so far, I must say that this is a large gap between the fields, which we are trying to reduce. It is important to talk about what has already been achieved, what are the intentions and outputs in the field of robotics and artificial intelligence. Sometimes people have completely unrealistic expectations of what is possible. There is also a lot of discussion about the dangers of these technologies, but we welcome that. There are fears that robots could take control of the world in any way. These discussions are interesting, but they are not about the dangers we would face in the coming decades. Specifically, artificial intelligence technologies are component technologies, offering individual tools for use in many areas, where machine learning methods can solve a number of specific tasks. If a large amount of data is available, it is possible to train systems with truly stunning results. But what is missing, of course, is the creative angle. Even if you have a large palette of oil paints, this does not mean that an image will be created. You still need human creativity to find new approaches and new ideas. That’s why there are artists. It’s not a question of replacing anyone with anything. Technology is a powerful tool, but it is mainly up to people to find an area where these tools will produce new results.