This Forbes interview was made possible thanks to the collaboration between RICAIP Testbed Prague at CIIRC and Continental, a technological leader in the automotive industry. Among other things, it introduces the RAASCEMAN project, in which several of our teams, particularly from DFKI and CIIRC, are actively involved.
The Continental Automotive plant in Brandýs shone in this year’s Global Lighthouse Network. The plant was awarded for its speed in implementing Industry 4.0 technologies. How did they manage to achieve this? In the latest episode of the Forbes BrandVoice podcast, Jakub Hamerník from Continental Automotive and Pavel Burget from the Czech Institute of Informatics, Robotics, and Cybernetics (CIIRC) at CTU discussed this success.
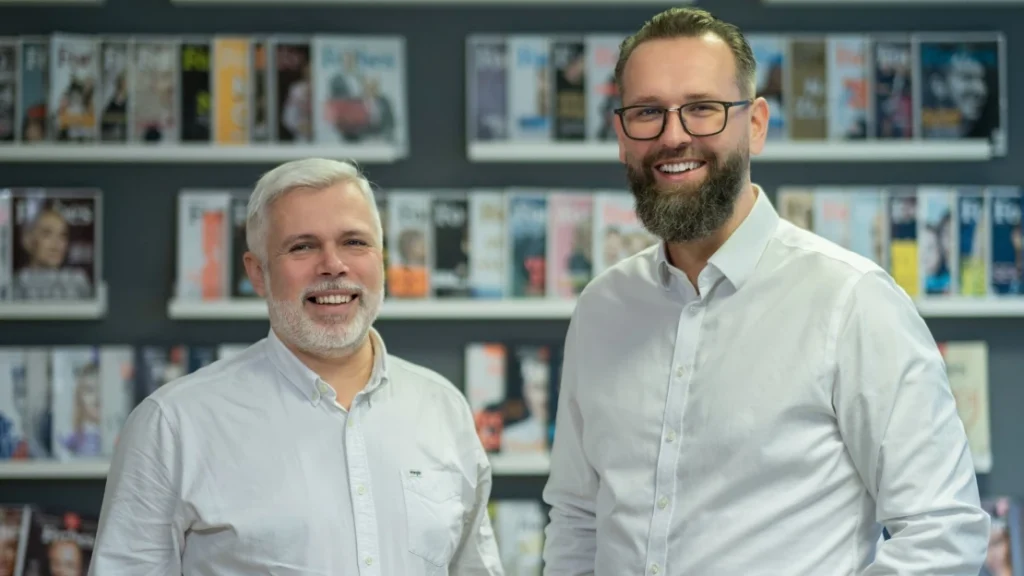
Photo by: Petr Krupička for Forbes
It’s not just about speed. Industrial companies are primarily focused on manufacturing efficiently and responding flexibly in real time to customer demands. At the heart of these efforts is the vision of smart factories, where people play the role of specialists. “Large companies have been aware of this for some time, but even small and medium-sized enterprises are beginning to realize they need to rethink how they manufacture, how they utilize human potential, and they are looking for new technologies that could be beneficial to their production,” says Pavel Burget, head of the Testbed for Industry 4.0 at CIIRC CTU.
Thanks to its partnership with CTU, Continental’s Brandýs factory succeeded in the international competition of the Global Lighthouse Network, an initiative of the World Economic Forum. The manufacturer of displays for modern automotive cockpits has thus joined the ranks of the most advanced companies in the world. “The competition was immense—800 plants entered the first round, and in the end, only 17, including us, were awarded. It’s a significant success for us; we’re the first plant within the global Continental network to achieve this,” said Jakub Hamerník, Smart Manufacturing Manager at Continental Automotive, in an interview.
The factory addresses its digital transformation and manufacturing through several projects, including RAASCEMAN, which develops software tools that enable companies to quickly and efficiently respond to unexpected disruptions. This project was supported by the European Commission with €4.6 million.
What can such recognition bring to the Czech economy? What does full automation mean, and what role will humans play in it? Is it time to start thinking about the fifth industrial revolution? These were the topics discussed by Pavel Burget and Jakub Hamerník, and you can listen to their conversation in the audio below.
What Jakub and Pavel said in the podcast?
For our non-Czech speaking audience, we present the following text, which is an approximate transcript of the inverview with English translation, not a verbatim transcript. Even so, it captures the most important messages that the two gentlemen spoke about.
Does Europe have a chance to maintain and strengthen its production?
Jakub (Continental): To succeed in streamlining production processes, it is crucial to use human and financial resources much more efficiently to deliver a quality product to customers in the shortest possible time. The key is constant innovation.
Innovative technologies help precisely to increase efficiency. This also leads to an increase in know-how and employee involvement in production processes.
Pavel (CIIRC CTU): Even SMEs are looking for ways to incorporate innovation into their operations. The rising cost of inputs (energy, materials) is pushing companies towards higher production efficiency. The trend is to use digitization platforms and technologies for data collection and simulation tools. Virtual manufacturing can better prepare real production.
What is the Continental’s approach?
Jakub: We focus on data collection from existing production lines and data analysis to analyze problems. If you solve, say, 50% of the problems you have in production, you can be more efficient and plan resources better.
Since 2020, Continental already has a talented team of data and digitization engineers who can work with the technology and apply it in practice.
Data is everywhere and there is a lot of it. If you can’t understand the data that describes your production process, you’re still lost. That’s why it’s important to include process experts in your data analysis who can describe how the process works. A data analyst will select the right data and evaluate it accordingly. Artificial intelligence can help a lot in this.
Continental’s journey focuses on these three main currents:
1. Big data (or as we call also “one version of truth”)
2. Smart automation
3. Automation of logistics processes
What is the main product produced in Brandýs n.L?
Jakub: The Brandýs plant is responding to the change through the influence of electromobility, where the infotainment in the cockpit of the car is becoming a central element for the end customer. We supply fully digital, virtual cockpits for (electro)cars, which are large-format displays in the cockpit.
Our end customers are the big car companies.
Why do we need to build more resilient and customizable production?
Pavel: To reduce errors, the human factor, to respond to labour shortages. Inefficiency and inefficiency mean additional costs.
Jakub: To deliver the right number of units of product at the right quality to our customers.
How does more resilient production come about?
Pavel: That’s what Testbed for Industry 4.0 is for, where at CIIRC we connect theoretical results and approaches with practical applications focused on industrial production. We have an overview of what the latest approaches and research directions are, for example in the field of artificial intelligence for manufacturing and robotics, as well as through collaboration with other research teams. At the same time, we are aware of the needs of industry, such as manufacturing that is resistant to various influences that, for example, disrupt the timeliness and continuity of deliveries. These are topics that we are addressing in the RICAIP project, for example. Thanks to this European project, we have been able to equip our testbed with the latest technologies.
“Manufacturing as a Service” (MaaS)
Pavel: One of the research directions addressed in RICAIP is “Manufacturing as a Service” (MaaS). We focus on making it possible to produce a product without being concerned, from an external customer’s point of view, with how and where the product or part will be produced. We can think of it as a network of manufacturing companies that are interconnected. That network is itself capable of delivering the product. It provides the service of that production.
“MaaS” is a vision for the future, we are not there yet. It is a concept that is being discussed more and more often, and it is being mentioned even at the level of the European Commission’s research plans. One of the principles is to link up entire factories and production sites, which can be small subcontractors, in such a way that such a manufacturer is able to offer its service automatically. So that the company can offer what production means and the production capacity it has at its disposal. When a demand comes in within a network of factories connected in this way, the firm can automatically respond to that demand.
This concept involves both production capacities and supply chains. This makes the system very complex and gives it many variables. On the other hand, by linking the different nodes of the network, such as factories, suppliers, and logistics companies, they will be able to automatically agree among themselves on the best way to deliver the required product to the required quality at the required time and place.
How can an industrial company cooperate with a research institute?
Jakub: In principle, a laboratory such as the Testbed for Industry 4.0 at CIIRC CTU, prepares technologies for use in production practice. It simulates problems and their solutions.
We are already collaborating in two grant projects where our engineers are working together to solve problems such as the resilience of supply chains or, for example, 3D printing.
We’ve done multiple projects, getting to know one side and the other first. We’ve done end-to-end simulations of our products. We’ve also simulated errors that can occur in the manufacturing process. Moreover, we had a project to reduce energy consumption for robotic lines.
Pavel: We are now working together on a project called RAASCEMAN, funded by Horizon Europe. In addition to Continental and CTU, other partners are involved. Together, we are developing the concept of Manufacturing as a Service. Together with Continental, we are delivering one scenario specifically to increase the resilience of automotive production and the ability of production to respond automatically to changes that may disrupt production.
What is the RAASCEMAN project about?
Jakub: The project is planned for three years and includes all the necessary phases of defining the brief, where Continental can specify the problems for the whole consortium in relation to the supply chain. Continental will also outline to the others how these problems could be solved based on what it has learned so far. The whole consortium learns from Continental’s knowledge and can apply it to the final product of the project, a MaaS system for supply chains.
The actual testing of the solution will take place at the Brandýs plant, we will evaluate it together with the entire Automotive Group, and if the project is successful, we will roll it out to other Continental branches in the Automotive sector. In this respect, the Brandýs plant is a pilot plant.
Pavel: At the CIIRC’s Testbed, we are currently working on about five similar large-scale projects with companies, and in addition to that we have several smaller projects for a shorter period, which are aimed at transferring a known result from previous projects, which is already proven in our conditions, to the specific environment of a given company. Depending on the type of cooperation, our clients are both large companies and SMEs.
The RAASCEMAN example is a typical research project, where at the end of the solution after three years there will be a proof of concept. Thanks to Continental’s involvement, we can adapt the concept already in the development phase to what the production environment needs. From the moment a concept is verified in this way, it then doesn’t have to be a long journey to get it into real production.
The aim of these larger projects, funded by the European Union or national grant agencies, is to use public funds to develop a result that can benefit other entities, even smaller companies.
What is the Absolute Automation?
Jakub: Fully automated production lines, the logistics chain, but also automatic data collection and analysis, where the final worker, the engineer, receives the final data from the production and is able to react to problems related to automation, logistics or product based on this.
The role of people is in the form of a highly skilled worker who can understand, manage, adjust and maintain the automated unit, as machine maintenance is also required.
Pavel: The workforce we want to do monotonous work is dwindling in the labour market. That’s why we need to replace these activities with robotization, the involvement of artificial intelligence, the connection of sensors and control systems. This is difficult because humans, even when performing monotonous and repetitive work, are adaptable compared to robots, and can react to changes in the environment without thinking. This is what robots and artificial intelligence systems have to learn. This learning is complex and we can never teach a system to respond to everything. However, with the development of artificial intelligence and the means and power of computers, possibilities are opening up in ways we could not have imagined just a few years ago. Less skilled labour will become less important in the production process, but skilled workers who can set up, modify and maintain complex systems will become more important.
Global Lighthouse Network Award for Continental
Jakub: Continental has been awarded the Global Lighthouse Network award by the Davos-based World Economic Forum (the award was presented on January 20, 2025). In practice, this means that the Continental production site in Brandýs has become one of 173 global leaders from 30 countries among production sites that focus on Industry 4.0 innovation and the implementation of new technologies. We won the award in the category for the manufacturing sector, which includes the automotive, medical, arms industry, logistics and a great variety of other types of production, not only automotive.
This award assessed our plant as a whole, although the functioning of production was demonstrated by specific examples of how technology works. The nomination process that we had to go through also broke down the IT structure, our strategic partners, how we develop our staff, how many staff were promoted, and the positive impact of the key identifiers within this Global Lighthouse Network and the application of new technologies.
The first round of the Global Lighthouse Network in Phase 12 involved 800 manufacturing sites globally and only 17 were successful, less than 2%. Brandýs site of Continental was one of them. This is a great achievement for us, we are the “first Continental” to do so.
We want to continue to develop new technologies, which is what this award continues to motivate us to do. This award is also a bit of a commitment to further collaboration within the community, to develop the technology while opening the door to potential new members of the Global Lighthouse Network. That is why we are already preparing Open Days for smaller and larger companies in our plant, where we will show what we have already applied, what we have not yet applied and what effect it has had on our production process.
This very prestigious club not only inspires us, but we can also inspire others. In recent years, these lighthouses have been growing, especially in China, where there is a lot of investment. European plants are not so successful, but we have succeeded, for which we also have to thank strategic partners like CTU.
The inspiration passed on by former members of this community is mainly the development of key indicators over a larger time interval. New players within this network have a lot to give because they can share their experiences, what they have implemented and what it has brought them. The main thing is not getting a prize to put up, but getting the opportunity to consult technology trends with other companies in other industries outside of automotive. They may have different problems, but in practice, it often means using similar technology, applications, or processes.
The biggest challenges and milestones expected in 2025
Jakub: Within our sector, it will be the PLM system (Product Life Management) that will allow us to run production lines more efficiently in the future, where we will have all relevant data together in one platform accessible to all Continental employees worldwide. This is our pilot project, which must be successfully evaluated by November 2025.
Pavel: The biggest challenge is to successfully continue on the path of supporting small and medium-sized enterprises, which we embarked on in the past year thanks to our participation in a prestigious programme supported by the European Commission to introduce innovation and new technologies. Thanks to this, we are able to provide SMEs with the equipment we have in the testbed and help them verify the feasibility of a new technology or solution concept, whether it is suitable for their production or not. We are already working on several projects, and in 2025 we want to reach out to a wider group of companies and offer these opportunities. In this way, we will help to modernise Czech industry. The funding available in this programme makes it much easier for SMEs to start innovating. We are able to offer them the means to take the first step, overcome concerns about whether innovation is right for them and see if they can achieve a return.
How do you perceive Industry 4.0? And what about Industry 5.0?
Jakub: The first phase of Industry 4.0 was the pure automation of our production lines. The second phase is “advanced functionality”, i.e. data collection and analysis to streamline already automated processes and increase the competence of the workforce.
The main benefits of this second phase for the economy are greater possibilities for fast delivery, increased quality of supply and therefore increased sustainability, reduced energy consumption, and increased efficiency of people. Towards the east, sustainability is built on the low cost of its resources. Europe, on the other hand, is raising the price of energy and wages. Therefore, we need to bring industry to a state where it is more efficient, and consumes fewer resources, especially on the energy side, so that Europe can remain competitive.
Pavel: Rather, we are in phase two of Industry 4.0, and we may not even be done implementing all the ideas of Industry 4.0 that were introduced about ten years ago. It’s not just about manufacturing, but also about other areas of life and other aspects of society: how people are educated or how companies push their innovations forward. Industry 4.0 is still relevant and it will take time before it is fully implemented and operational.
Jakub: Whenever we think of Industry 4.0 or even more forward-looking Industry 5.0, it is important to choose the right strategic technological partners for the future as well, without them innovation can hardly happen.