On 5 March 2024, RICAIP joined the National Centre for Industry 4.0 (NCP4.0) and Deloitte and co-hosted a workshop dedicated to sustainability and ESG reporting in the premises of the RICAIP Testbed Prague, CIIRC CTU. The insightful presentations showed that data is the key to success and sustainability can act not only as a challenge, but rather as a positive opportunity to increase the efficiency of industrial production, across the entire supply chain. This event provided a good opportunity to showcase the recent research focus on developing solutions using advanced technologies and automation algorithms to relieve the demands of ESG reporting, especially for manufacturing companies.
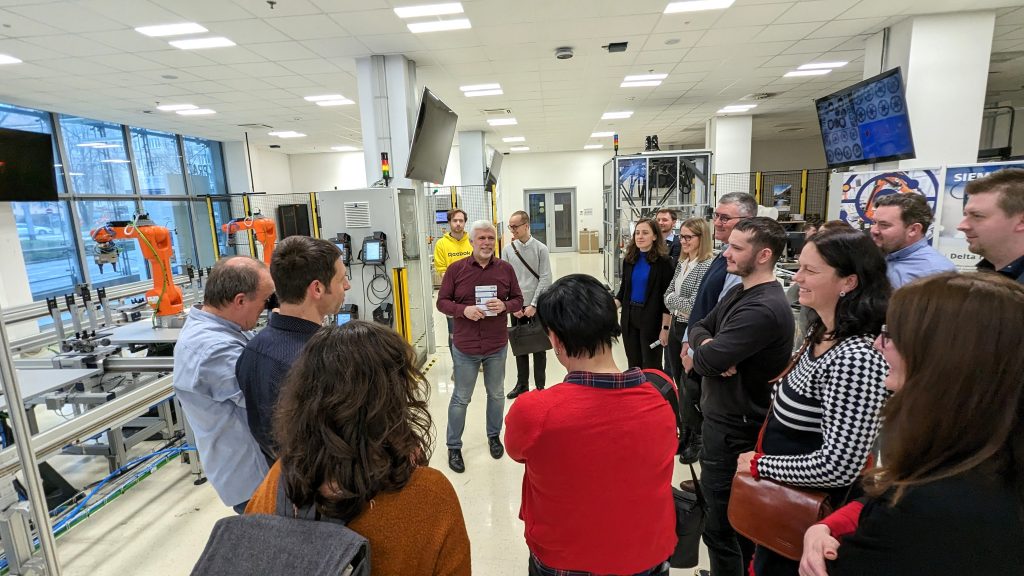
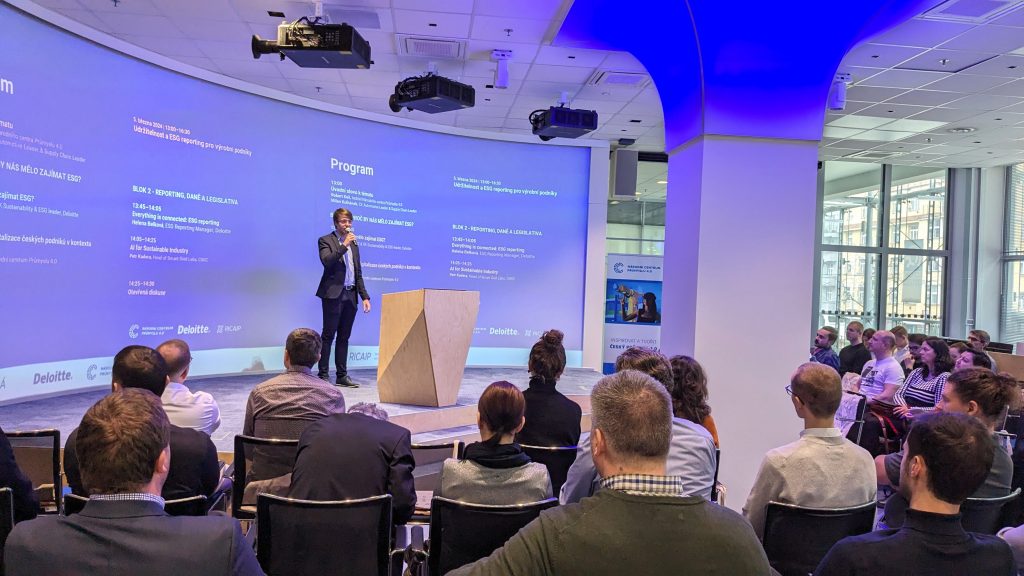
The CIIRC CTU teams with the use of the infrastructure of the RICAIP Testbed Prague are dealing with issues around the ESG reporting and the data monitoring and management needed for a complex transformation of industrial manufacturing towards sustainable development. They apply advanced methods and technologies such as as artificial intelligence and machine learning to offer solutions that are not only effective, but also have a positive impact, for example, on the competitiveness of companies.
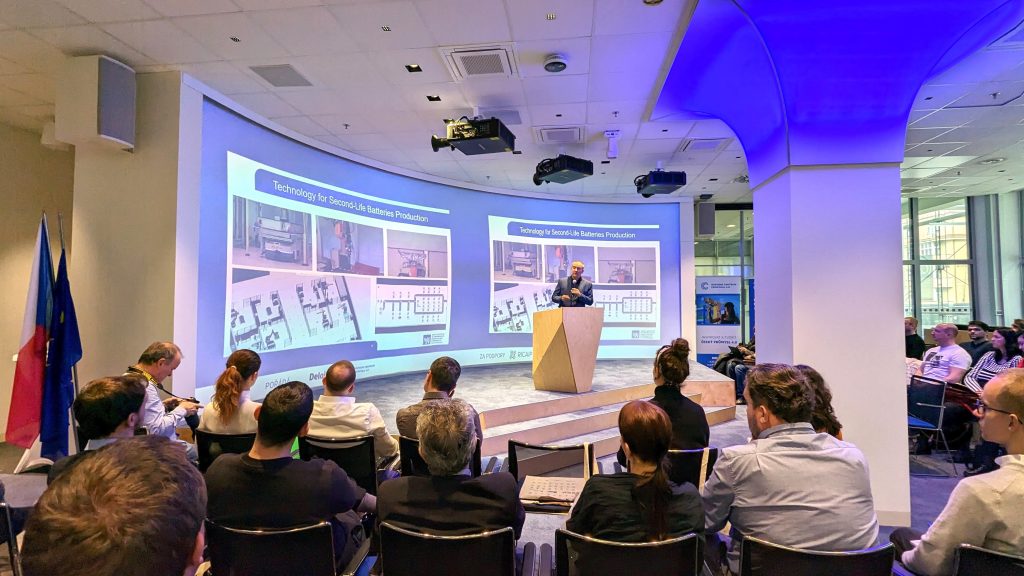
Petr Kadera, Head of Intelligent Systems for Industry at CIIRC CTU, pointed out that the AI-driven production transforms waste into valuable assets. Artificial intelligence is deployed for production quality control, diagnosis and maintenance and it provides a knowledge data basis that collerate a wide set of parameters of the product, detects anomalies – not individually for each parameters but in a complex manner.
He presented this approach, among other things, on the his recent project on automated factories for the retrofitting of end-of-life batteries from electric vehicles. Batteries that are no longer usable in cars due to reduced capacity can, after disassembly, repair and reconfiguration, serve for many years as a backup stationary power supply, for example for family homes.
Verification of the functionality of the proposed approaches using physical demonstrators was carried out thanks to the infrastructure of RICAIP Testbed Prague. The first phase included a virtual commissioning of the designed factory, which allowed to test the control systems and use virtual reality tools to gain insight into its operation (read also below).

During the guided tours in the RICAIP Testbed Prague, data collection for ESG reporting and production optimization was presented on the case of system for measuring power consumption on an industrial robotic line and evaluating important metrics in real time.
The RICAIP Testbed Prague teams are developing an automated integrated monitoring system to track the power consumption of industrial systems, transfer the collected data to a database for further processing and monitoring of input consumption. Using our experimental production line as an example, we demonstrate reporting principles for ESG reporting that can be applied to production halls and entire companies.
The basis for ESG reporting is data from real production. ESG indicators can be continuously updated and summary reports can be automatically generated from them. In addition, the system will provide instant visibility of consumption-related problems, which can lead to production and maintenance optimisation and other data-driven improvements.
Virtual commissioning of a robotic line for the automatic disassembly of batteries for electric vehicles is the recent study conducted in RICAIP Testbed Prague. The researchers deal with the use of suitable battery modules for secondary applications such as stationary battery storage based on the principles of flexible production control with automatic planning of production operations. They introduce the virtual commissioning of a single robotic cell, its realistic design and the connection of simulated robotic cells to a production line.
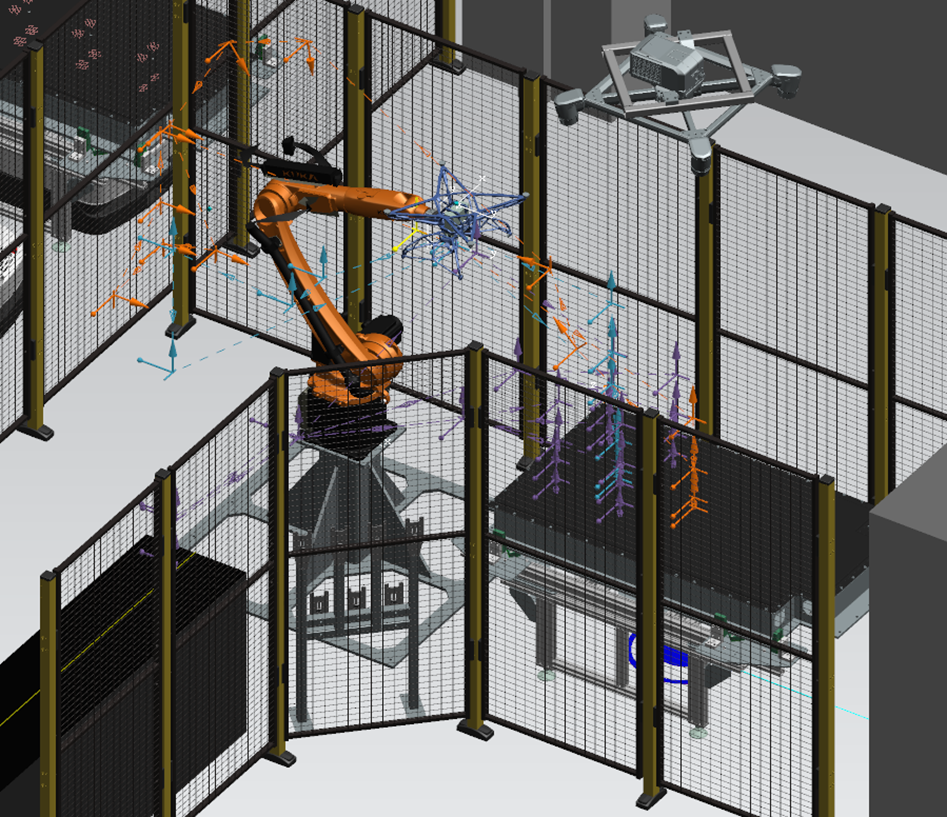
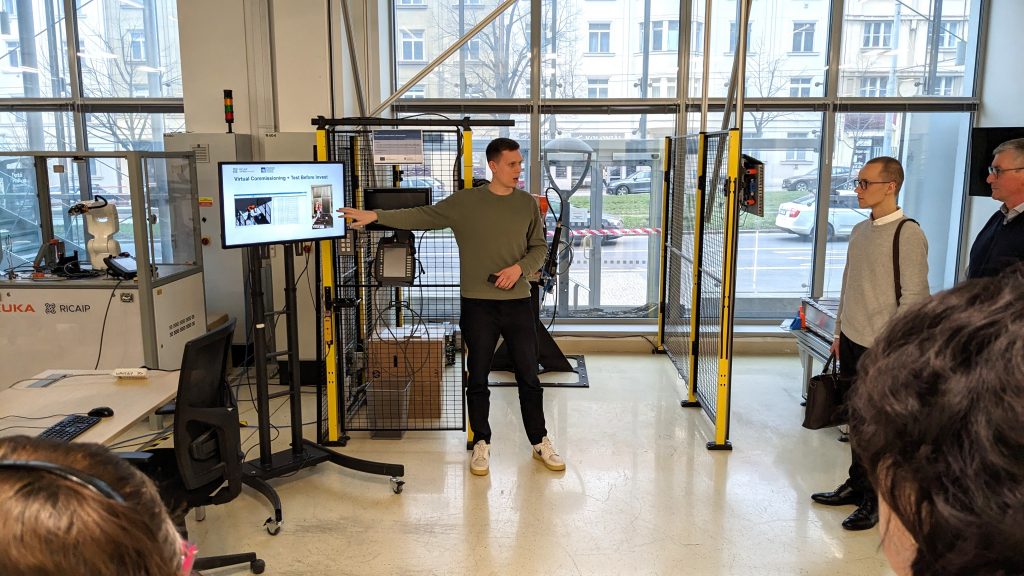
The flexible production control system, which can be linked to both the physical cells and the simulated line, allows to automatically generate sub-operations and ensure their execution.
Its flexibility lies in the fact that it can automatically react to any unplanned change without the need for manual rescheduling.
Photo gallery
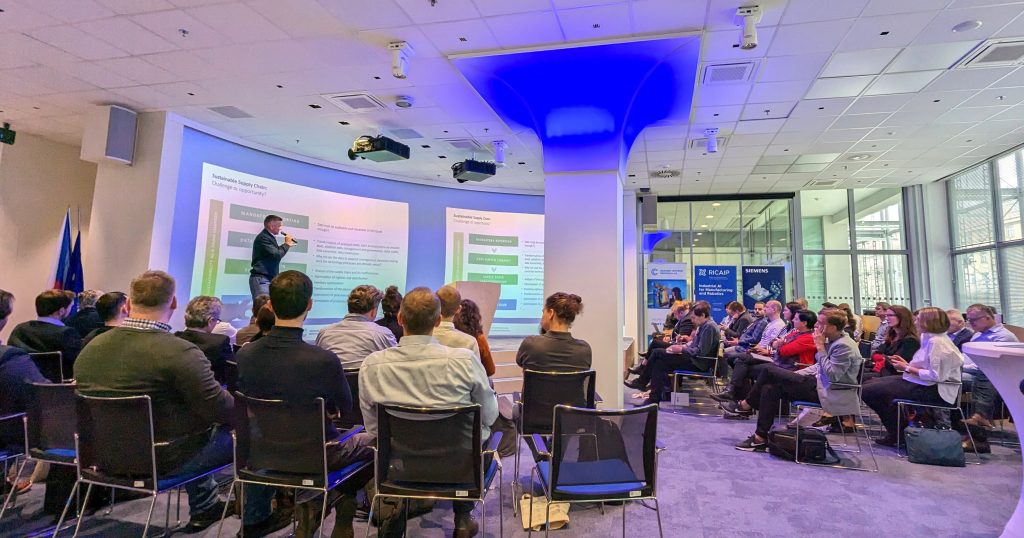
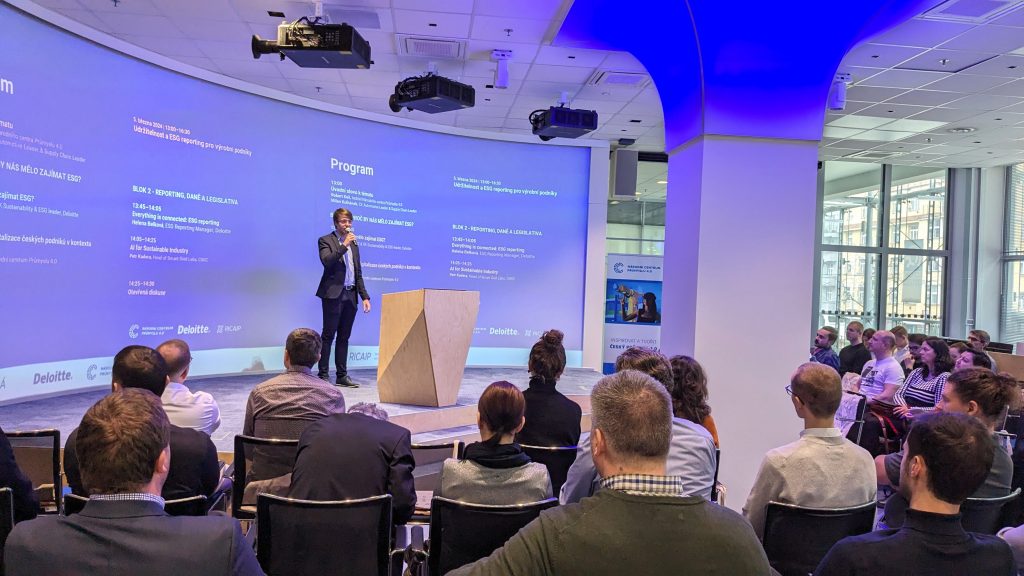
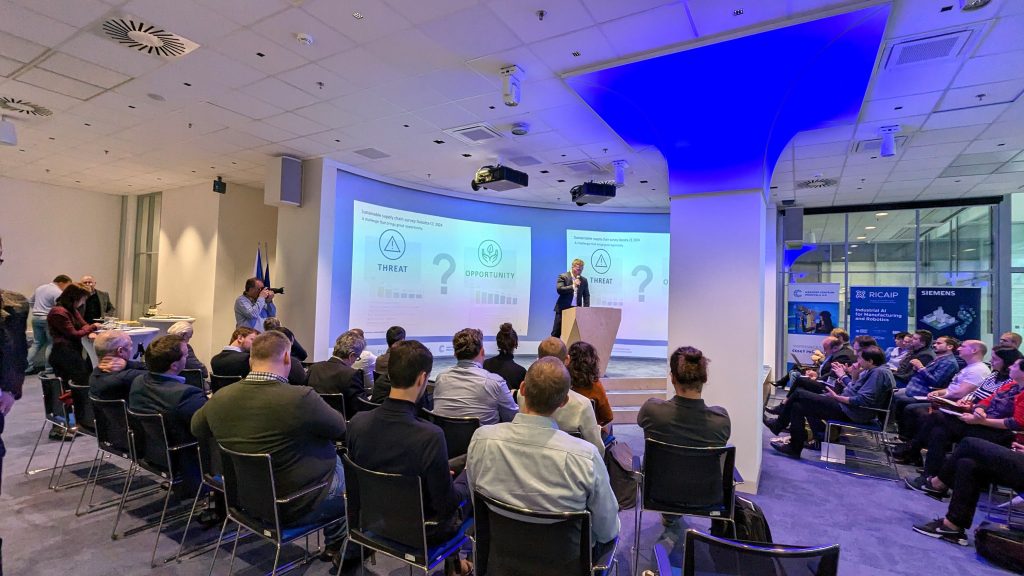
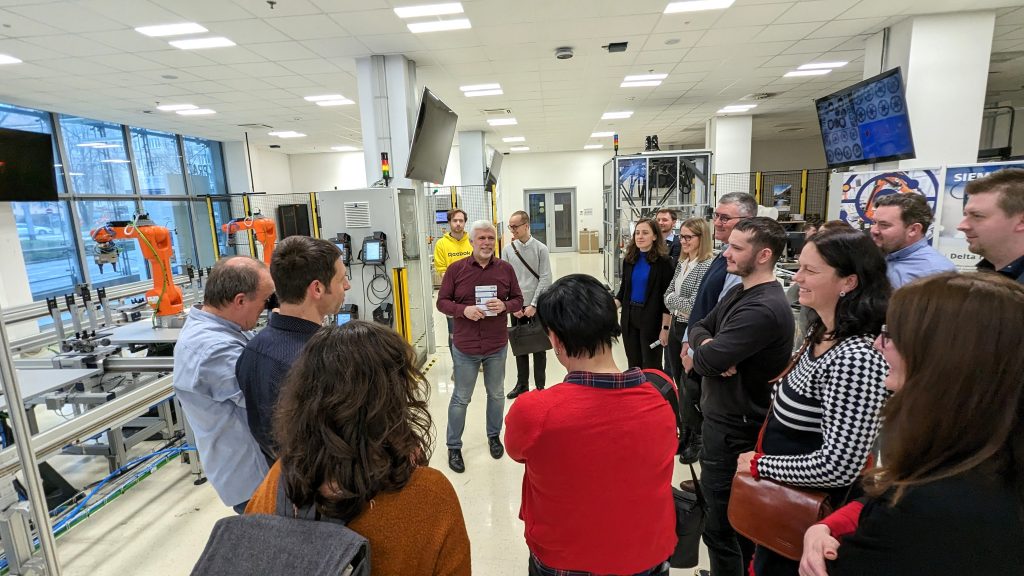
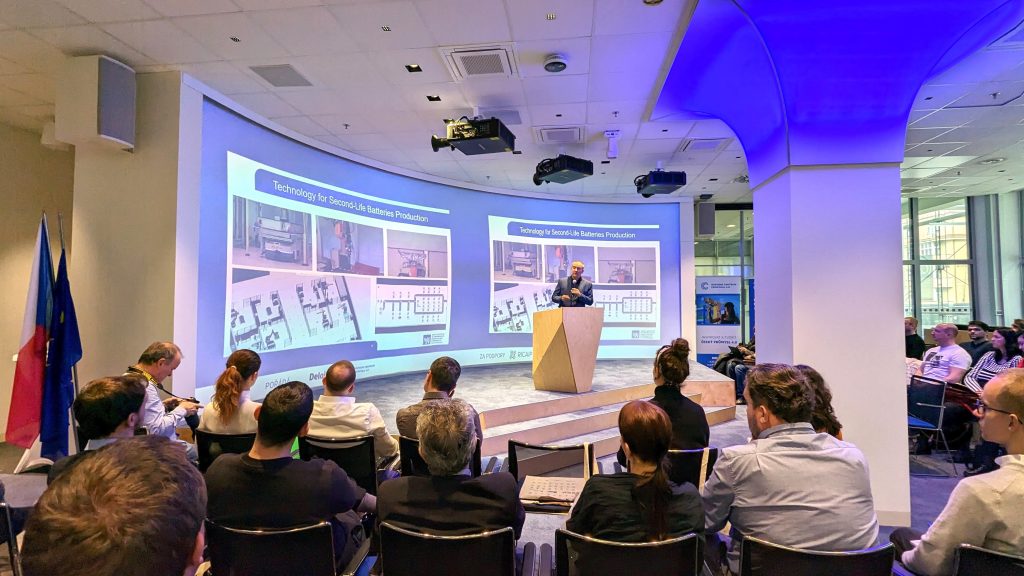
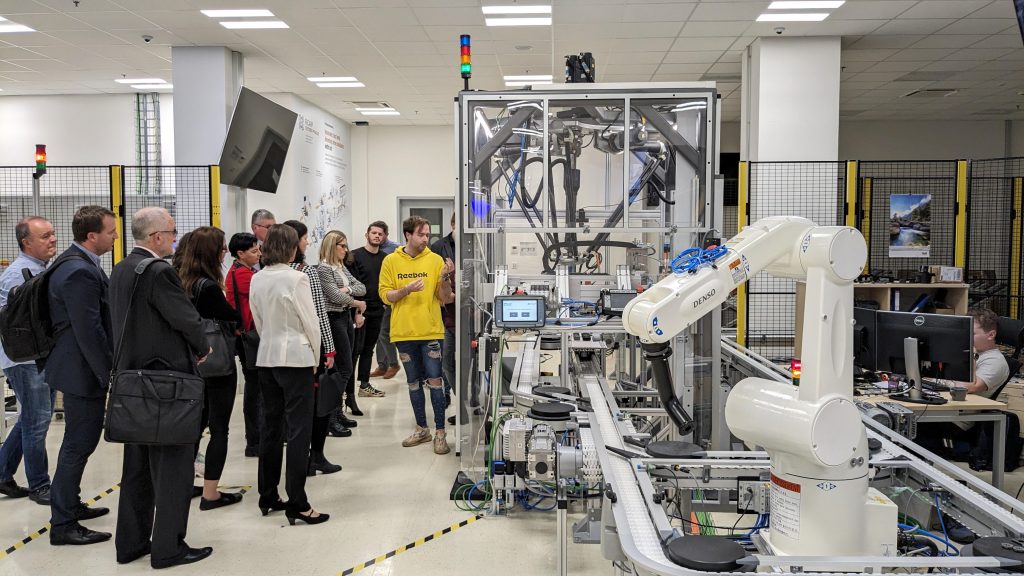
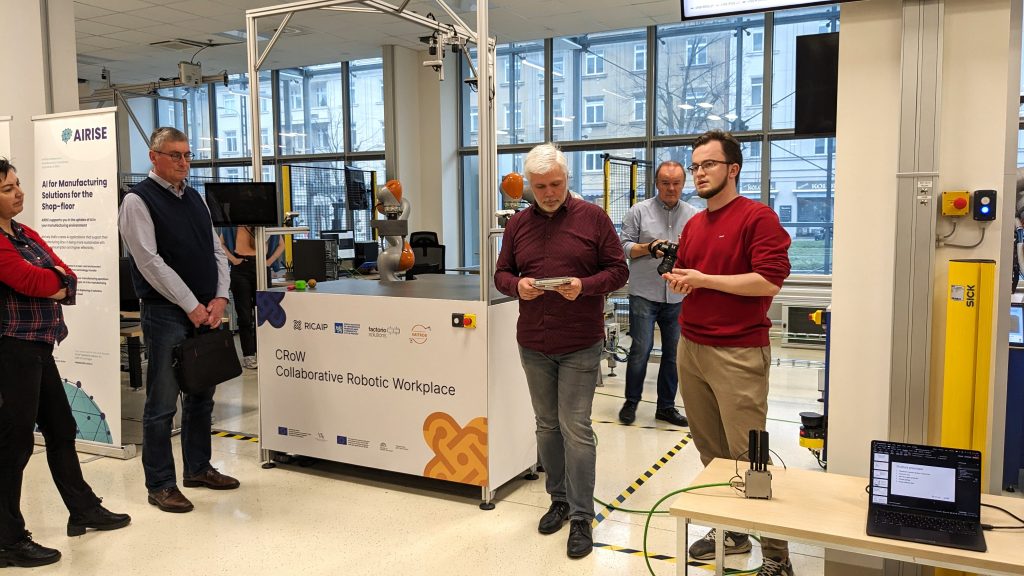
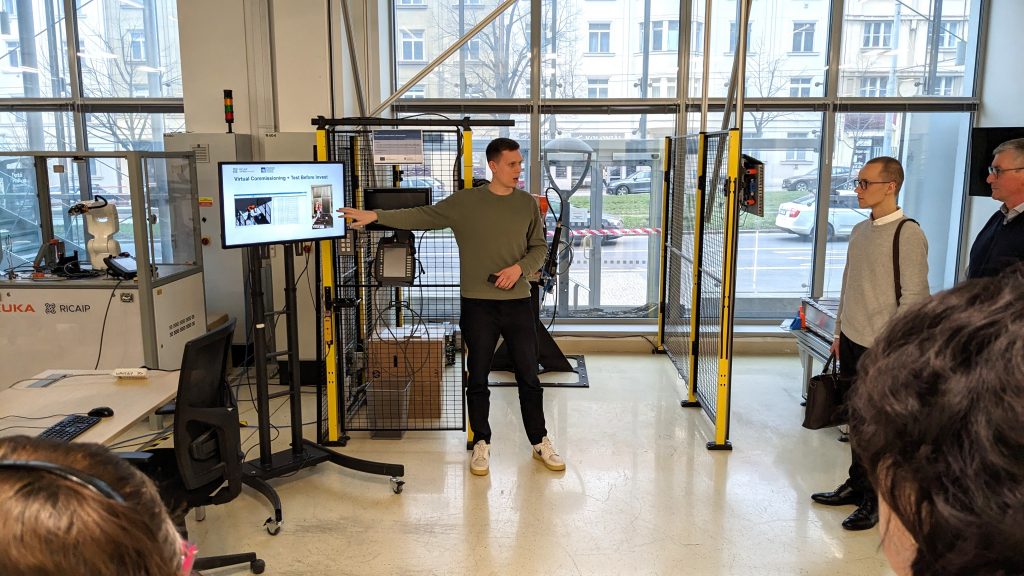

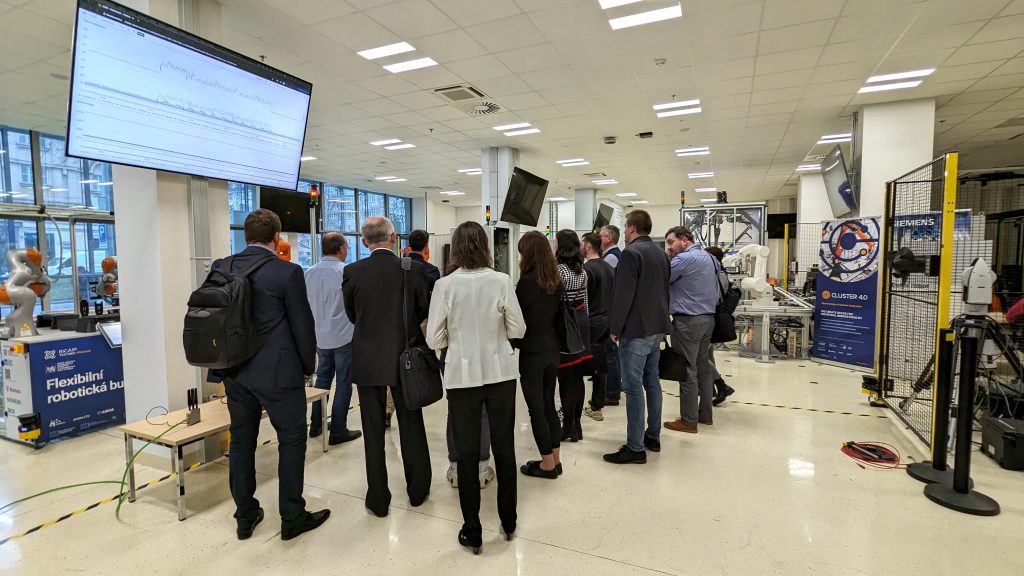
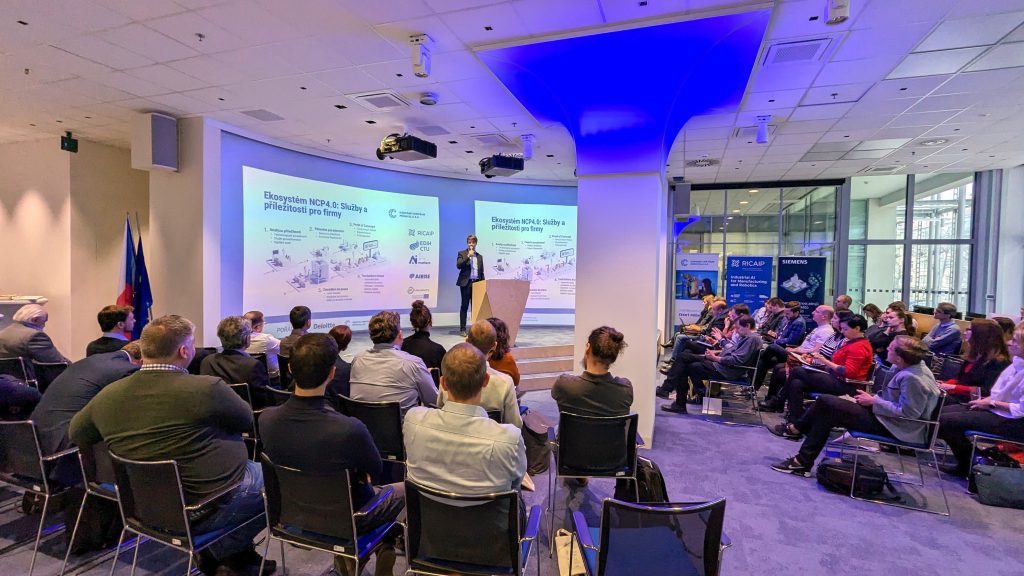