Author: Jan Markovič, Hospodářské noviny
Read the article that was published based on an interview with Pavel Burget, Director of the RICAIP Testbed for Industry 4.0, CIIRC CTU in the Hospodářské noviny (Economic Newspaper) on 2 October 2023 in regard with the exhibition at the International Engineering Fair MSV Brno 2023:
The graceful movement of the robots on the production line gives the impression that they are alive. But every single position of the smart hand has so far had to be carefully programmed to make everything run like clockwork. With the advent of machine learning and computer vision, however, the situation is changing. The robot no longer needs to learn exactly where to reach, but rather to know what to reach and why, thus becoming autonomous. And this is exactly the innovation that Testbed of the Czech Institute of Informatics, Robotics and Cybernetics (CIIRC) at CTU is now going to demonstrate at the joint exhibition of the National Industry 4.0 Centre at the Engineering Fair.

The focus of the exposition will be a robotic cell, which in a scaled-down form will realistically show how autonomous robots can replace monotonous human work in the near future where it has been necessary so far.
“We will show a cell with two robots that together disassemble a model of a battery for an electric car. They can unscrew the lid, check that all the modules have sufficient capacity and replace the bad ones with new ones. Then they screw the lid back on,”
describes the basic function of the robotic cell Pavel Burget, Director of the RICAIP Testbed for Industry 4.0, CIIRC CTU in Prague.
This is not a demonstration that was created just for the exhibition, on the contrary, it is a project for the Slovak company ZŤS Výskum a vývoj in cooperation with DEL company. So even though only a scaled-down version of the cell will be on display at the fair, it should soon become part of the real line.
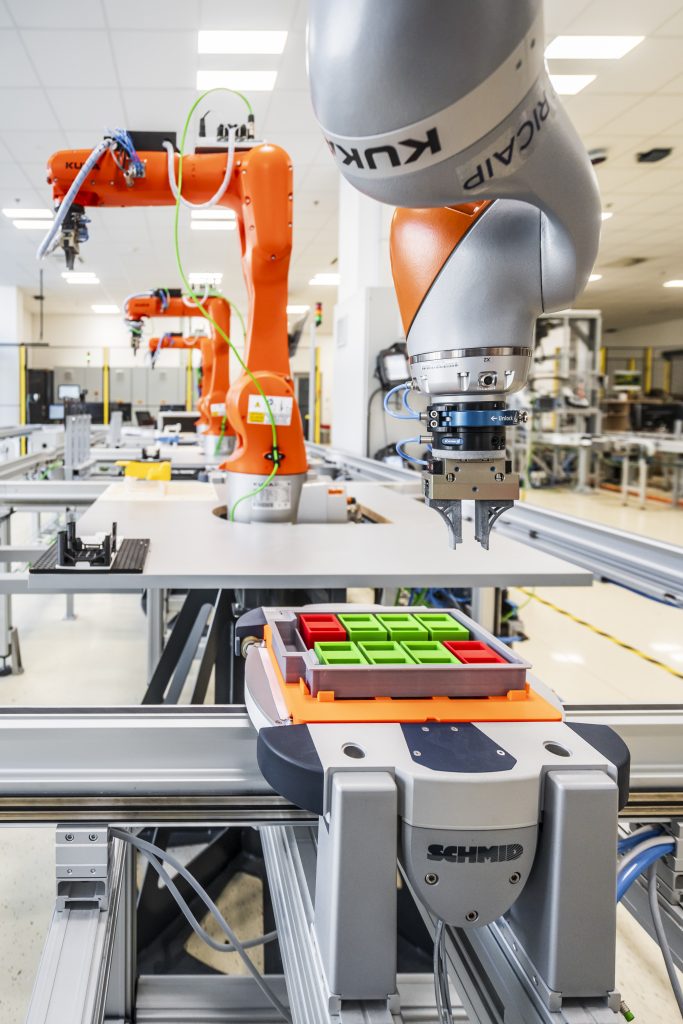
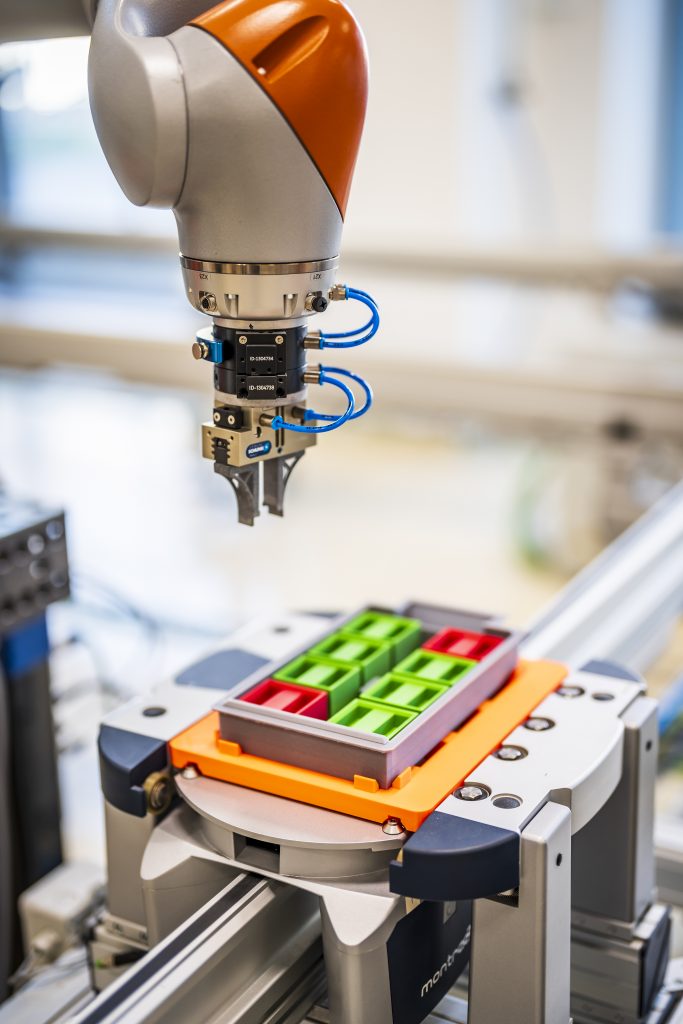
“During the development, we tried to make the robots as autonomous as possible, i.e. to do as much work as possible without human intervention. That’s why they are equipped with a 3D camera, and each robot also has one of its own. This makes it capable of more precise guidance when handling a battery or when screwing, which it guides itself with its screwdriver. We wanted to achieve that one robot would position the battery, even if inaccurately, and the other would work on it without any problems,”
explains Pavel Burget
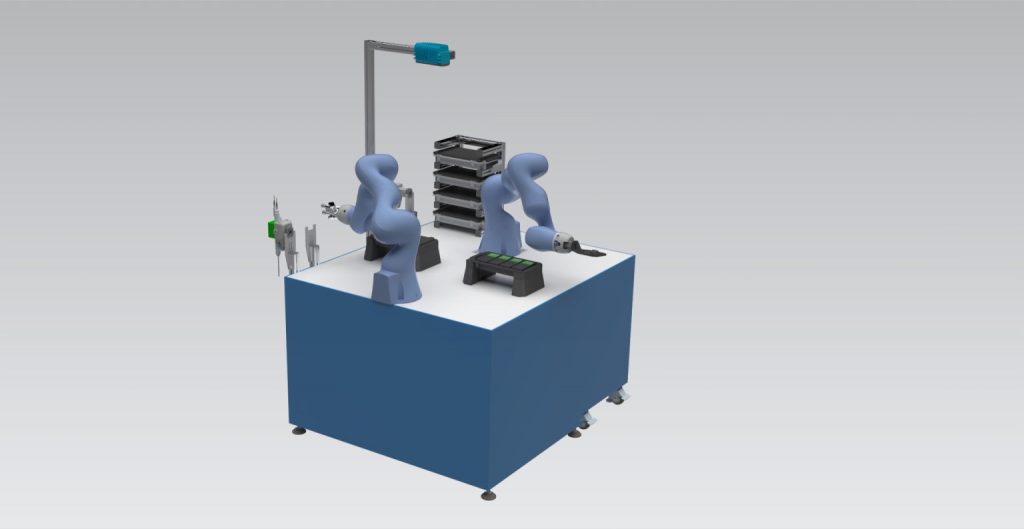
A robotic cell with two robots working together to disassemble a battery model for an electric car. They can unscrew the lid, check that all the modules have sufficient capacity and replace the bad ones with new ones. Then they screw the lid back on.
CIIRC has also focused on the flexibility of the cell. The robot that disassembles the battery stands still, but the robot that lays the battery is on a moving table with wheels. It can therefore be moved from place to place as and when it is needed.
“In practice, it’s a machine that needs to have parts put in or taken out. That’s what humans do now, but it’s a fairly monotonous job, which is why a lot of companies are trying to find solutions to get rid of it. In the case of our cell, the robot is a kind of warehouse that stacks and unstacks battery modules,”
adds Pavel Burget, the head of the Prague researchers.
The stationary robot is in turn equipped with a measuring probe and detects how the individual battery modules are doing. It doesn’t matter whether they are all in good condition or whether some of them need to be replaced. It can plan a new procedure for each situation and then work accordingly. Moreover, it doesn’t even matter what type of battery it is. Thanks to the 3D camera, the robot can recognise the different types. The goal is to be able to work with batteries that do not even exist today. It can simply handle it.
Put it anywhere, it just needs a signal
The development of a robotic cell takes a really long time, and it all starts in a virtual environment.
“The first phase is to prepare the algorithms that will allow the robots to operate autonomously. Whether it’s recognizing the position of a screw, gripping a housing, unscrewing modules, separating them into good and bad. Then it’s about physically verifying the algorithms and confirming that the robot is capable of autonomous operation,” Burget says, adding that the simulation in the virtual environment is far from over. Because the cells are modular, it is envisaged that an entire robotic line with perhaps ten cells working together will be in production.
“In the simulation environment, we can design and plan the entire layout of the line and not limit ourselves to just one cell. The layout and number of robotic lines involved, including the material flow, is designed automatically using a tool developed at CIIRC. Everything is linked by a production control system that generates a production plan.”
Pavel Burget
But the autonomous robotic cell project is changing another established practice. Typically, machines and control systems on production lines have to be connected via a hardwired link. But here, each cell is equipped with a 5G router. And it is 5G that will enable full data transmission of the industrial communication protocols Profinet and ProfiSafe, which are used in production. The data is processed on the server, so there is no need to have a complete computer at the robot. All this greatly increases flexibility. It can be placed virtually anywhere in the production process, as it only needs a signal to reach it. And thus it can be used in other operations where it is needed.
Pavel Burget also points out the advantages of modularity. “For example, we show a cell with two robots, but we are not limited in any way. More than one can work together at the same time, if necessary. This brings a lot of variability. Similarly, there is no limitation on what they have to parse. We show the electric car battery model as an example of a sustainable solution for the second life of these cells, but it’s all about getting the algorithms to learn the parts that the robots have to handle. And it doesn’t have to be just disassembly, of course, they can also handle the insertion and assembly of parts, and the position of the part can be different each time. It is enough that the robot can orient itself in a given situation, insert the part and then check back that it was inserted correctly,” says the researcher.
Pavel Burget also points out the advantages of modularity. “For example, we show a cell with two robots, but we are not limited in any way. More than one can work together at the same time, if necessary. This brings a lot of variability. Similarly, there is no limitation on what they have to parse. We show the electric car battery model as an example of a sustainable solution for the second life of these cells, but it’s all about getting the algorithms to learn the parts that the robots have to handle. And it doesn’t have to be just disassembly, of course, they can also handle the insertion and assembly of parts, and the position of the part can be different each time. It is enough that the robot can orient itself in a given situation, insert the part and then check back that it was inserted correctly,” says the researcher.
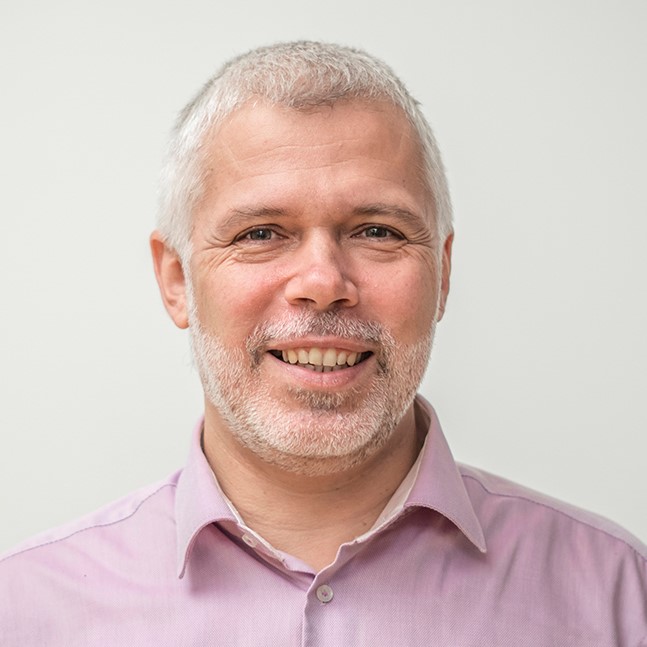
Speed thanks to 3D printing
To manipulate the parts, so-called grippers are needed, i.e. grippers or attachments that allow the robots to handle individual operations. For example, they use a drilling or suction attachment or an attachment equipped with a measuring probe to dismantle the battery of an electric car. Throughout the process, the robots can of course change the individual grippers depending on which one is needed at the time.
The CIIRC is working to be able to automatically design the necessary grippers and produce them using 3D printing. “This is what will make it possible to produce parts orders of magnitude faster than when they are made from welded structures. Usually it takes several weeks, but we can do it within a few days,” Burget points out.
RICAIP Testbed, together with other partners of the National Centre for Industry 4.0, will be showcasing a number of other innovations in manufacturing at its stand. For example, there will be augmented reality training for workers, where they will see how to work on a specific part thanks to special glasses. There will also be a so-called digital twin of the robotic cell, on which it will be possible to try out its virtual operation. This is already a convenient way to try out different production scenarios without interfering with operations and to prepare for changes in production or even just for expansion.
The article was published in a special supplement of HN Strojírenský veletrh.