Trends, visions, technological innovations and practical solutions under the Industry 4.0 umbrella developed in the environment of industrial testbeds. These were the themes of the Industry 4.0 Open Day, an event which took place on Wednesday 29 May 2024 and opened the premises of the RICAIP Testbed Prague at the CIIRC CTU to directors and managers of manufacturing companies, offering nearly two hundred visitors a series of discussions on digitalization, automation or production optimization. Testbeds at the technical universities in Prague, Brno and Ostrava work together to create an infrastructure that is ready to respond to current and future challenges in manufacturing. Many companies have already tried it out, while many are just learning about the possibilities offered by these workplaces.
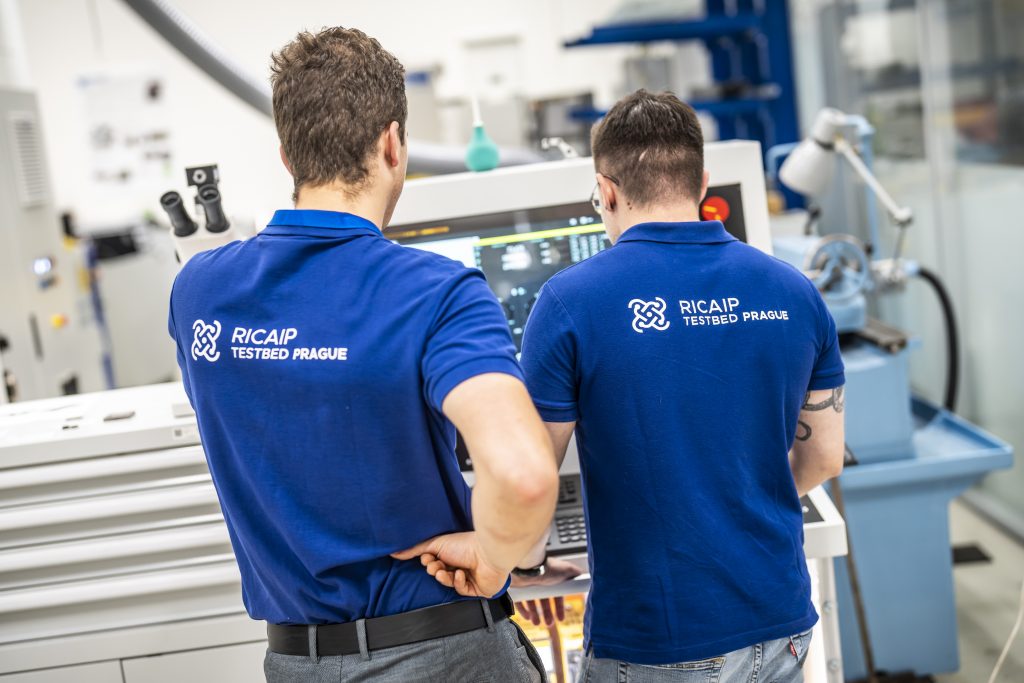
The event was jointly organised by the National Centre for Industry 4.0 (NCP4.0), the Research and Innovation Centre on Advanced Industrial Production RICAIP and the Czech Institute of Informatics, Robotics and Cybernetics of the Czech Technical University in Prague (CIIRC CTU). The aim was to present a wide range of practical examples and opportunities that are currently available to companies when introducing innovations and new processes. The testbeds, i.e. experimental laboratories at the CIIRC CTU in Prague, CEITEC BUT in Brno and VŠB TUO in Ostrava, are mainly trying to help solve the challenges that companies face.
According to the latest Analýza průmyslu 2024 | Analysis of the Czech Industry, which is prepared annually by NCP4.0, the top priorities of industrial companies include the pressure to accelerate the launch of products on the market, improve their quality and, last but not least, the need to be able to respond to changing customer requirements and be able to adapt products accordingly. According to DESI (The Digital Economy and Society Index), which assessed the digital performance of European SMEs, Czech companies were just below the European average in 2022. In 2023, the results improved slightly, but Czech firms still fell short of the European average. Compared to the previous year, however, there was a huge 20% increase in firms’ IT experience. Czech companies have clearly embarked on a trajectory of digitisation.
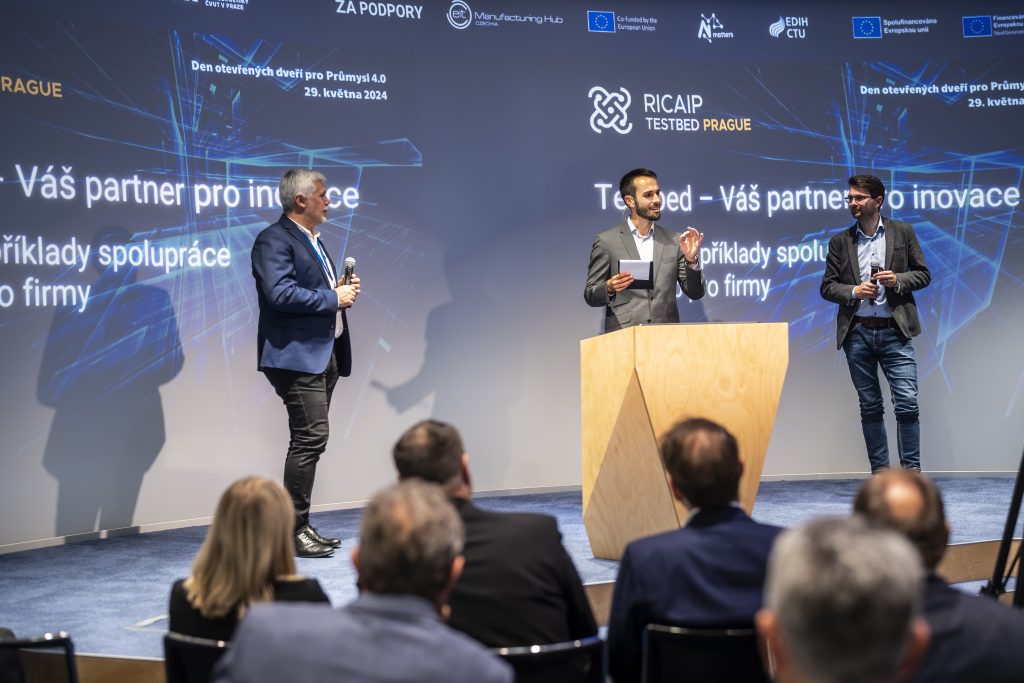
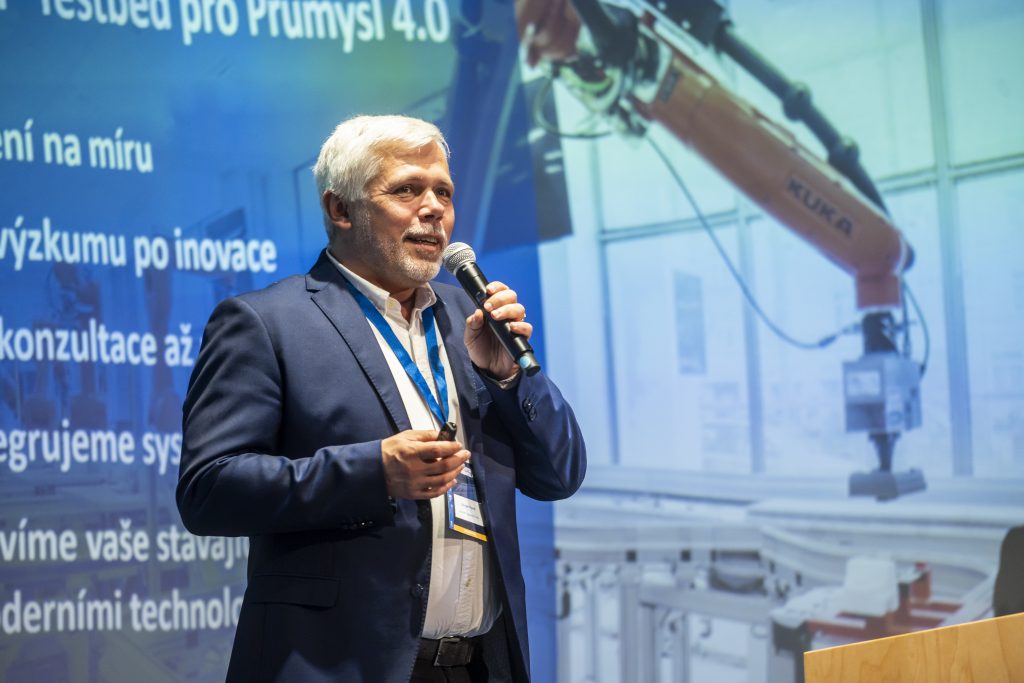
“This creates a potential where testbeds can help companies in a real and effective way,” says Pavel Burget, Head of RICAIP Testbed Prague at CIIRC CTU, adding, “We provide tailor-made solutions for companies, from research to innovation, from consultation to preparation of documents for integrating solutions into production. For example, we can help develop models for autonomous robot decision-making for a desired production task and safely test them before a company invests expensive resources in commissioning. We also help break down other barriers – for example, by training workers to be able to adopt and work with new technologies.”
Companies can take advantage of the state-of-the-art equipment that the testbeds are equipped with, as well as various support programs and subsidies, thanks to which they can receive comprehensive professional services with up to 100% discount. The three testbeds are connected to the RICAIP centre as well as the EDIH and AI-MATTERS TEF (Testing and Experimentation Facilities) networks, which are currently two key schemes that the European Union and the Czech Ministry of Industry and Trade are using to support the adoption of digital technologies and AI for SMEs.
“Innovation is demanding on company resources, financial, technological, time and human. The testbed acts as a playground where new solutions can be tested before the company actually invests its money in their full implementation. Thanks to this, innovations are more accessible, less demanding in preparation and implementation, and companies can apply the results of university research directly into industrial practice,” confirms Ondřej Beránek, coordinator of the Czech Testbeds node within AI-MATTERS.
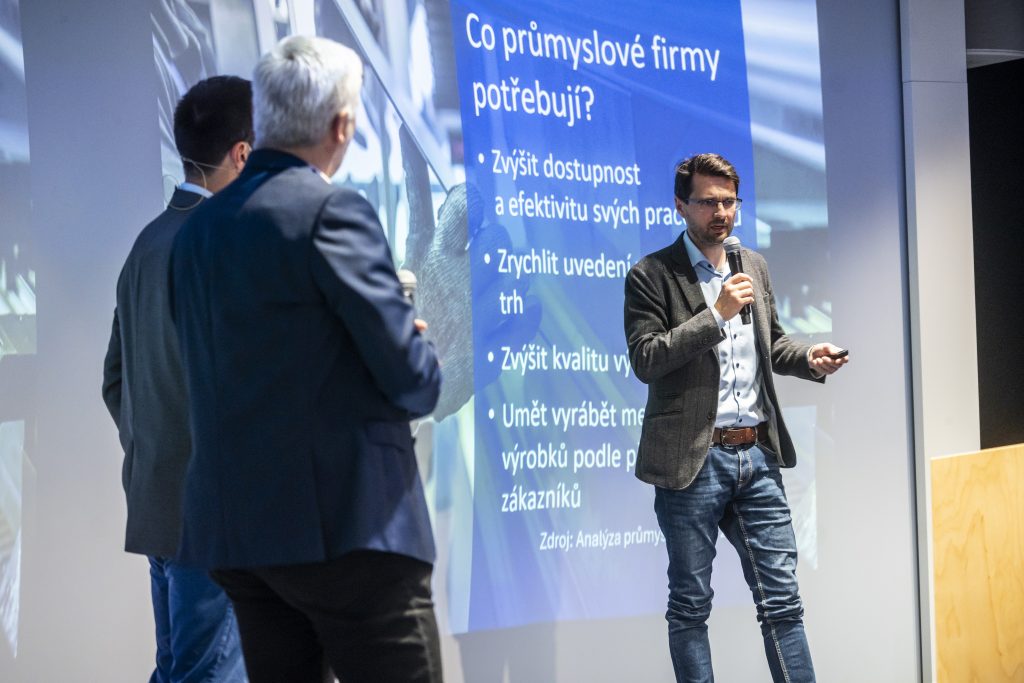
RICAIP Testbed Prague proves that the principles that work in production are transferable to other sectors, specifically agricultural production. “We are developing the VITISPECTOR software solution for a winemaking company in the field of precision agriculture,” says Pavel Burget, introducing the service supported by the EDIH CTU, “Thanks to a comprehensive software module using machine learning, the winemaking company will be able to better plan what sprays to use, in what doses and when to use them to properly protect the vineyard.” This will have a real impact on reducing the ecological burden caused by plant protection. The system evaluates meteorological and climatic data in combination with specific vine disease occurrences and will also enable automated and targeted production control. The data will be recorded and traceable, allowing both easier reporting resulting from strict industry and ESG regulations and the creation of an individual pedigree for each bottle accessible to the end customer based on the batch number.
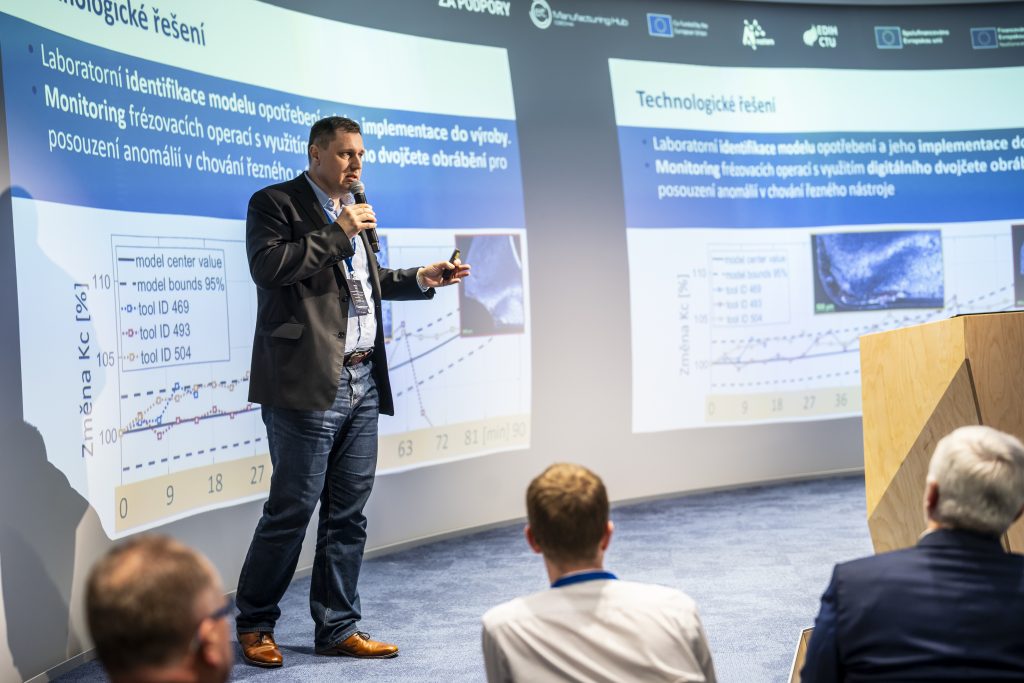
“In cooperation with an engineering company, we focused on the use of data analysis and sensorics to reduce costs,” said Petr Kolář, Deputy Head of the Department of Industrial Production and Automation – IPA CIIRC CTU, presenting another example from the field of industrial practice. “By default, machine tools are replaced after a fixed period of time, regardless of their actual state of wear,” explains Petr Kolář and continues, “Our team has developed new computational models that help to automatically determine the wear of machine tools. When a defect is detected, the system removes the defective cutting tool from production earlier so that it does not cause scrapping of the workpieces. Conversely, it will keep a tool that can perform well in the cut longer in the process and prolong its use.” The data is also used for mandatory ESG reporting.
Through EDIH DIGIMAT, the RICAIP Testbed Brno team contributes to a solution for a small manufacturing company focused on visual inspection of production quality. “Our goal is to develop a model to ensure high reliability in detecting deviations in product dimensions and surface data,” explained Pavel Václavek, head of the Cybernetics and Robotics research group at CEITEC BUT. “It can also happen that a product will have a defect that was not known in advance.” RICAIP Testbed Brno prepares datasets for training AI models using artificial intelligence, verifies suitable sensing technologies for different scenarios in production taking into account real conditions including light and dust conditions and tests the whole concept. For this purpose, among other things, it uses the new computing power of the NVIDIA HPC system that CEITEC BUT has recently acquired to enable the provision of this type of services to companies.
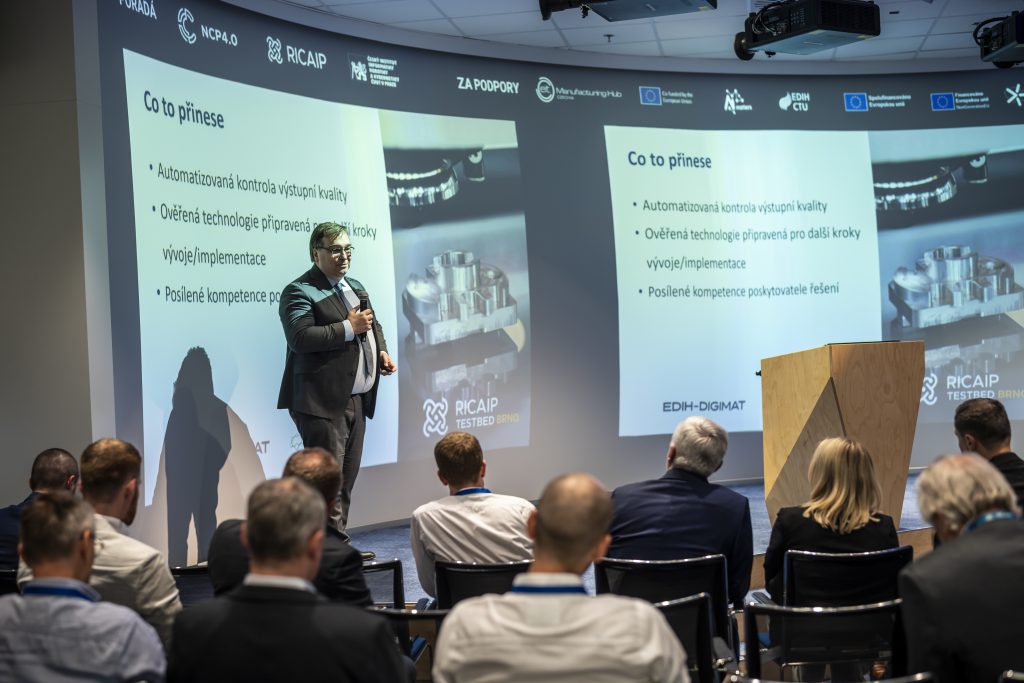
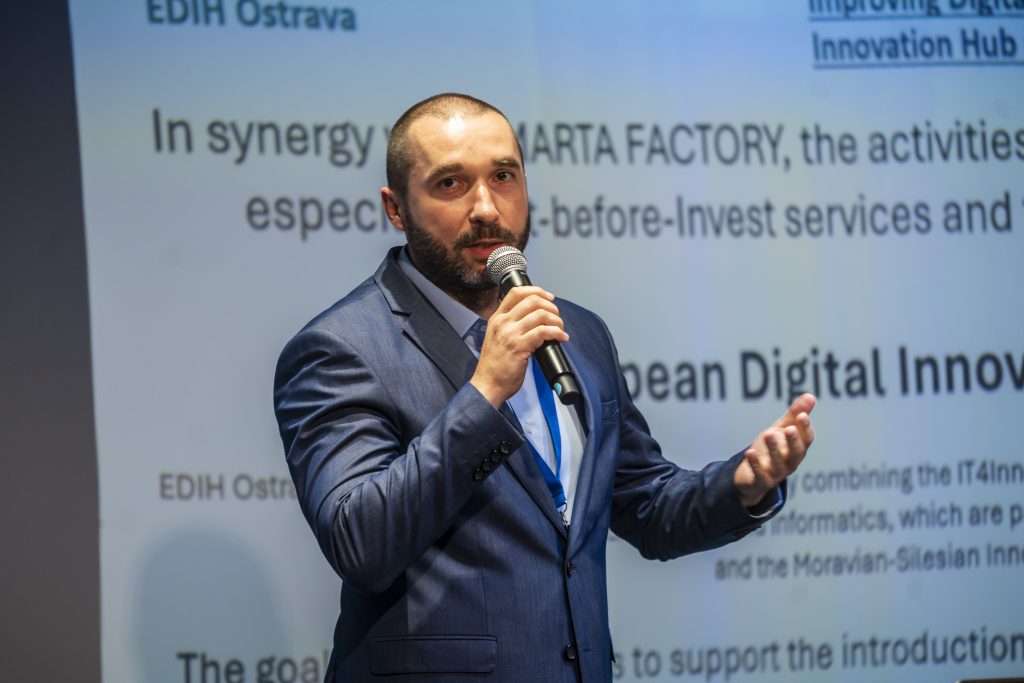
“In the Ostrava testbed, we have created a digital twin in the Tecnomatix Plant Simulation environment for sheet metal fabricators and manufacturers of machine parts to optimise and plan production line processes,” Petr Šimoník, Vice Dean for Cooperation with Industry at the Faculty of Electrical Engineering and Informatics of the FEI VŠB-TUO, introduced the specific “test before invest” service of EDIH Ostrava for the company NC Line.
“At NC Line, they had data from sheet metal production and processing, but needed to be able to better plan and optimize production to increase the efficiency of the production process. The “Smart Factory” team, led by Dr. Macháček, managed to create a digital twin and connect it to their ERP system, which now allows for long-term planning of machine and human activities and continuous optimization of the entire production process,” added Petr Šimoník. The company now has e.g. materials management within production and human resources management connected to the system and can more easily look for bottlenecks and problems that may occur on the production line. Every day, it is possible to run a model based on the current data for production and retrain the types of activities on the production line in advance and constantly update production planning using the digital twin.
Testbeds collaborate with technology providers and industry leaders at the national level through the ecosystem of the National Centre for Industry 4.0 and at the international level through other projects and initiatives, in particular the European Innovation Community EIT Manufacturing, which extends the range of different support programmes for innovation deployment. The participants of the Open Day for Industry 4.0 at the CIIRC CTU thus gained a comprehensive picture of technological, expert and subsidy opportunities.
Photos: Jiří Ryszawy
Photo Gallery
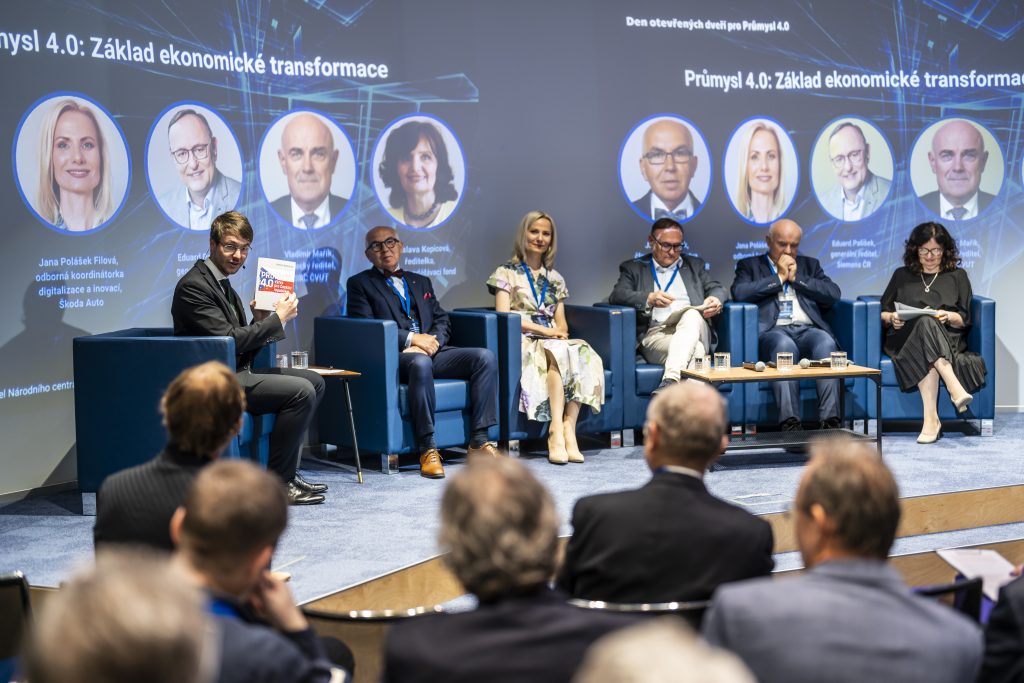
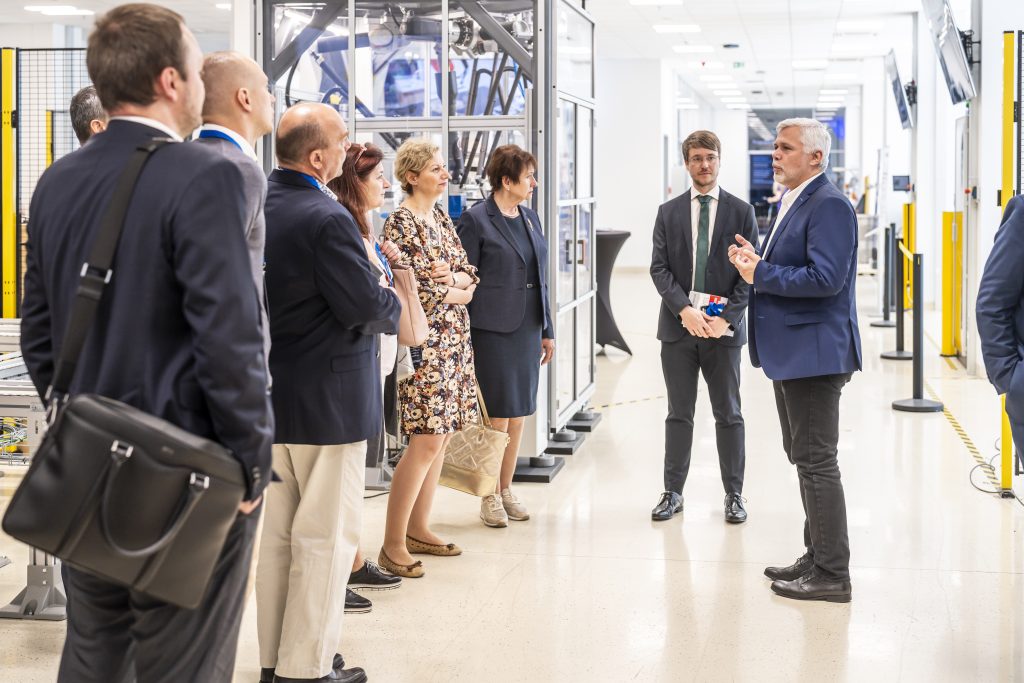
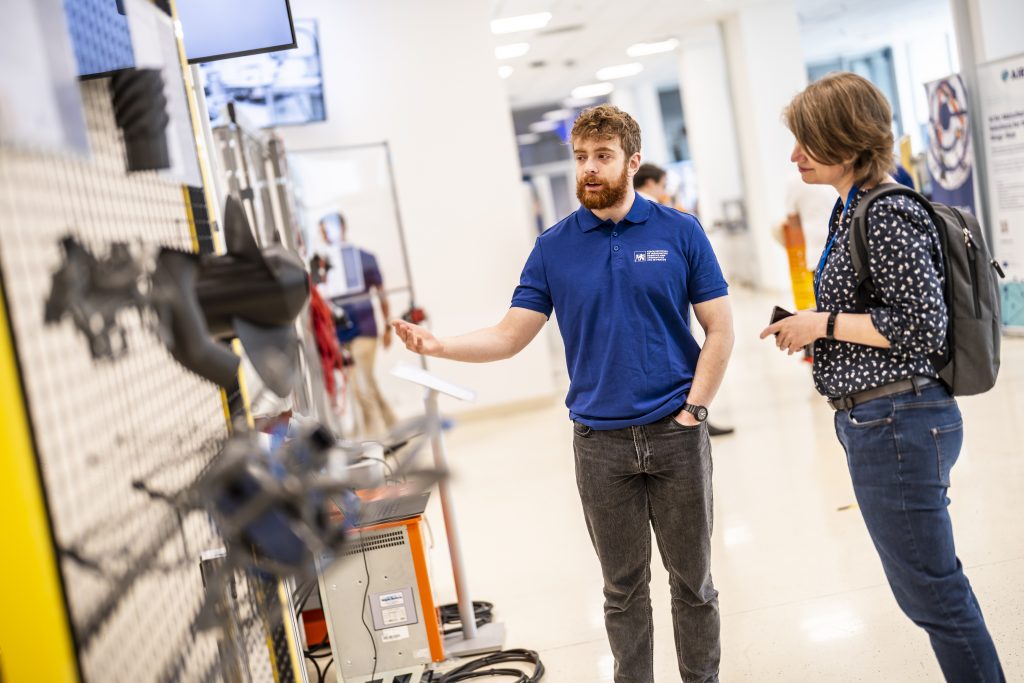
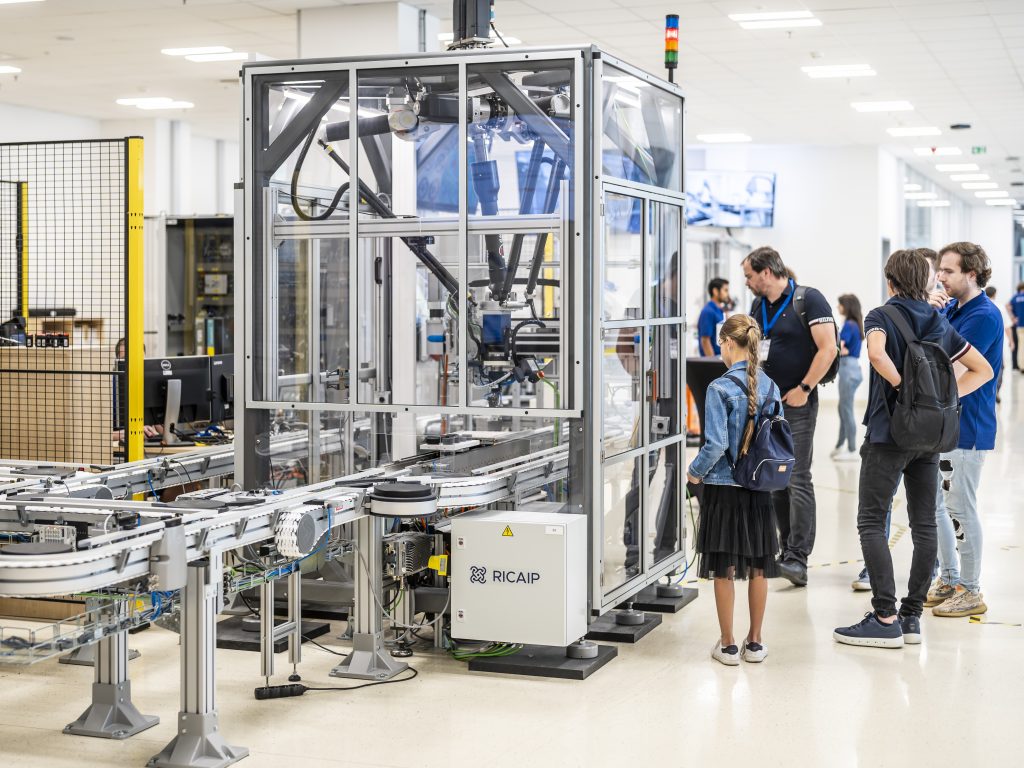
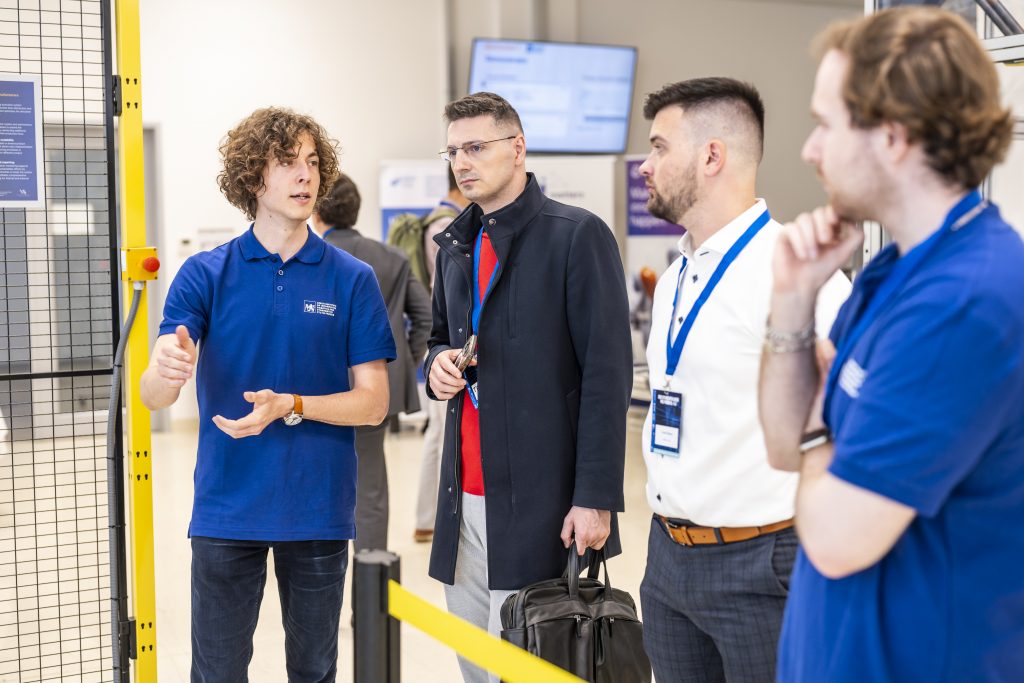
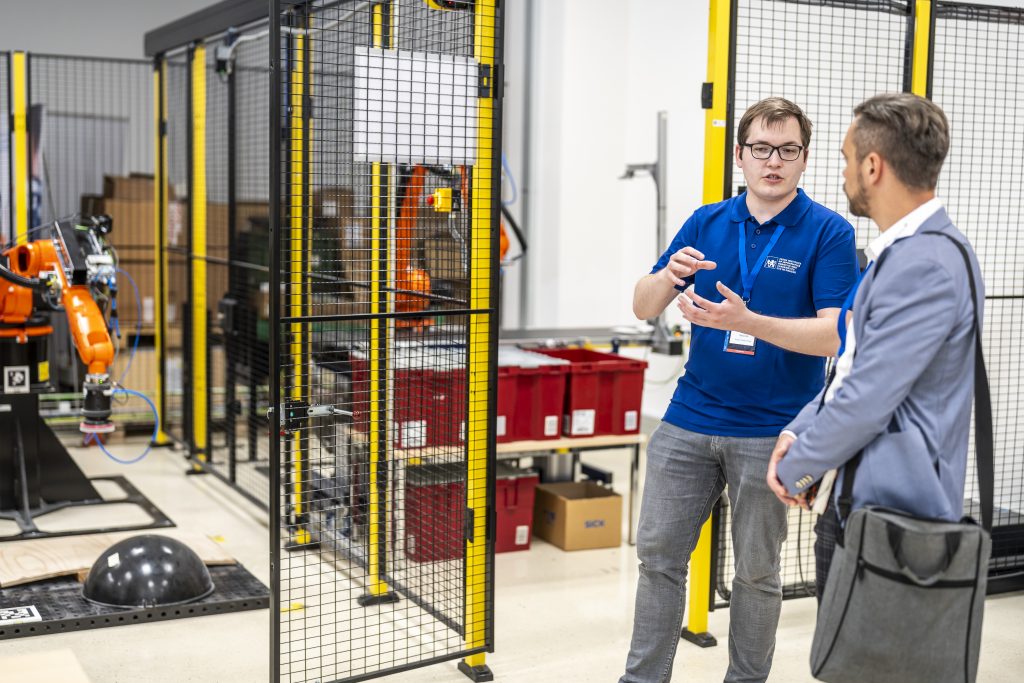