Author: Ing. Matúš Kozovský, Ph.D. (Researcher for SW development, CEITEC BUT)
A comprehensive system for measuring and real-time detection of interturn short-circuits was demonstrated within the project AI4DI – Artificial Intelligence for Digitizing Industry in the BUT Industry 4.0 testbed facility in December 2021. An essential element of the whole demonstrator is a special PMS motor with configurable winding. The machine is connected as a dual three-phase machine. With the help of this motor, it was possible to measure and analyse the behaviour of the motor during different types of internal short-circuit faults. The obtained data were used for neural network training as well as for a better understanding of faulty motor behaviour. The neural network prepared in this way is able to identify internal short-circuit faults in the motor.
The whole demonstrator consists of a dynamometer, the special PMS motor connected to a dual three-phase power inverter, and NVIDIA Jetson AGX Xavier. The Jetson Xavier module is also used to accelerate neural network inference and visualize extracted features and operating parameters in real-time.
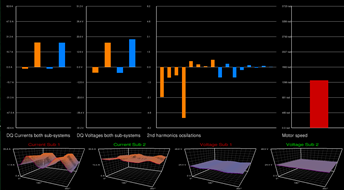
average time for fault detection, including communication delays and preprocessing time, is less than 2 ms. Neural network processing itself consumes 1.1 ms. This time is sufficient to protect the machine against additional thermal damage caused by short-circuit currents. The demonstrator thus shows the possibility to design a fail-operational system using a properly designed dual three-phase machine and advanced control algorithm in combination with a fast fault detection system.
