RICAIP aims to
To develop research excellence through a set of comprehensive use case studies serving as role models and demonstrators for future applications of the RICAIP principles of multi-site & distributed advanced manufacturing in the most relevant industrial sectors (aircraft, automotive, and production technologies).
And to advance the possibilities and benefits of Industry 4.0 and digitization in pilot use case studies and demonstrators. These use cases and demonstrators will prove the feasibility and enable a test and transfer environment for the industry.
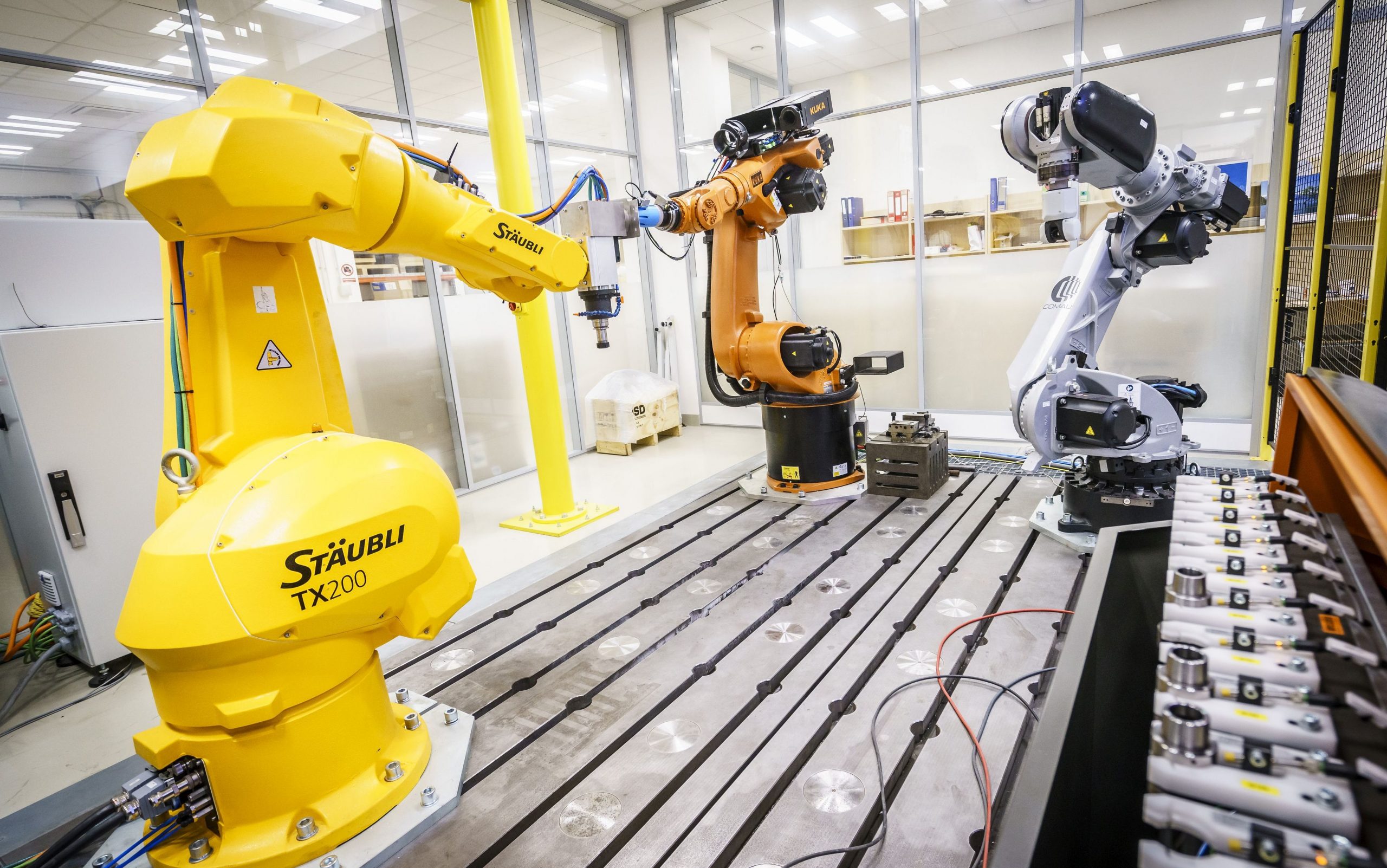
Following use cases will be developed

Distributed production sites
with various levels of mutual integration

Production as a Service (PaaS)
RICAIP Demonstrators
Flexible Production
The scenario will rely on connecting the customer’s choice directly into the production process. In such a way, the production will adapt itself to the product to be produced. The following key features are important:

The customer’s choice is analysed automatically

Production planning is done based on the customer’s choice and available resources

The production resources are commanded according to the result of the production planning
The production planning algorithm can also be used to plan the disassembly of the product. Traditional and collaborative robots are used to perform assembly and disassembly operations. A customer portal linked to an ERP and MES systems is used to receive the production orders and to track the status of the production.
Even though the assembly and disassembly operations are executed in one place, the system architecture is prepared for the distributed environment to be extended in the future. As an extension, a remote production site at CEITEC will be connected. This site will receive commands based on orders processed by the customer portal running in the ERP system.