Eighty scientific and industrial experts on robotics and industrial artificial intelligence (AI) from both sides of the Atlantic met last week at the Czech Institute of Informatics, Robotics, and Cybernetics Czech Technical University in Prague (CIIRC CTU) at the US-EU Workshop on Intelligent Manufacturing and discussed the aspects that would be significant for the next decade of the manufacturing in terms of scientific and technological development. The event was organised in close collaboration among three worldwide acknowledged personalities, Prof. Růžena Bajcsy from University Berkeley, Prof. Wolfgang Wahlster, DFKI, and Prof. Vladimír Mařík, CIIRC CTU. On this occasion, Prof. Růžena Bajcsy was also awarded two memorial medals. What are the main findings that will impact the industry and the path of R&D in robotics and manufacturing in the near future?
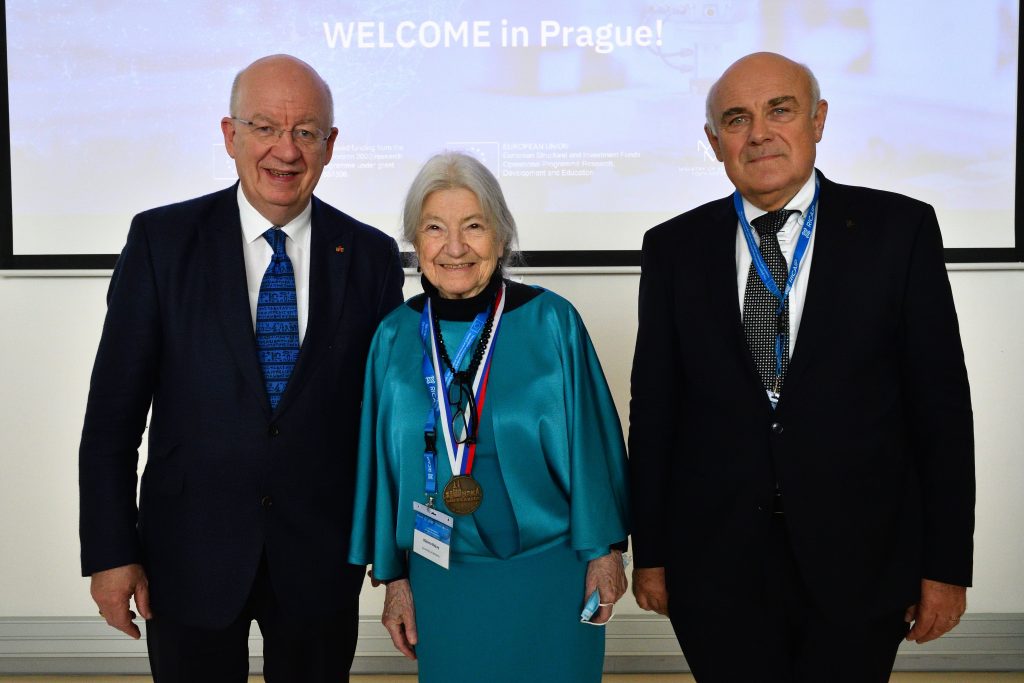
The idea to organise such an event in Prague matured over the last few years but could not be realised due to covid. The main pacesetter of this meeting was Prof. Růžena Bajcsy, a legend in the field of computer science and robotics in the USA with over 60 years of a rich scientific career.
“I was born in Bratislava at the time of Czechoslovakia, so I feel an affinity to the technological developments of that region.
Prof. Ruzena Bajcsy, UC Berkeley
It has been 30 years since both countries have enjoyed democracy. My intent of this workshop was to expose the Czechs and Slovaks and also the EU to what is going on in the USA and vice versa in the context of new technological developments as they relate to manufacturing.“
Prof. Bajcsy pointed out that the closer intersection of robotics and manufacturing in the Industry 4.0 agenda would only enhance the whole enterprise. Her words were also confirmed by Prof. Wolfgang Wahlster, one of the three inventors who introduced the principles of Industrie 4.0 ten years ago, founder of and Chief Executive Advisor at DFKI, the German Research Centre for Artificial Intelligence.
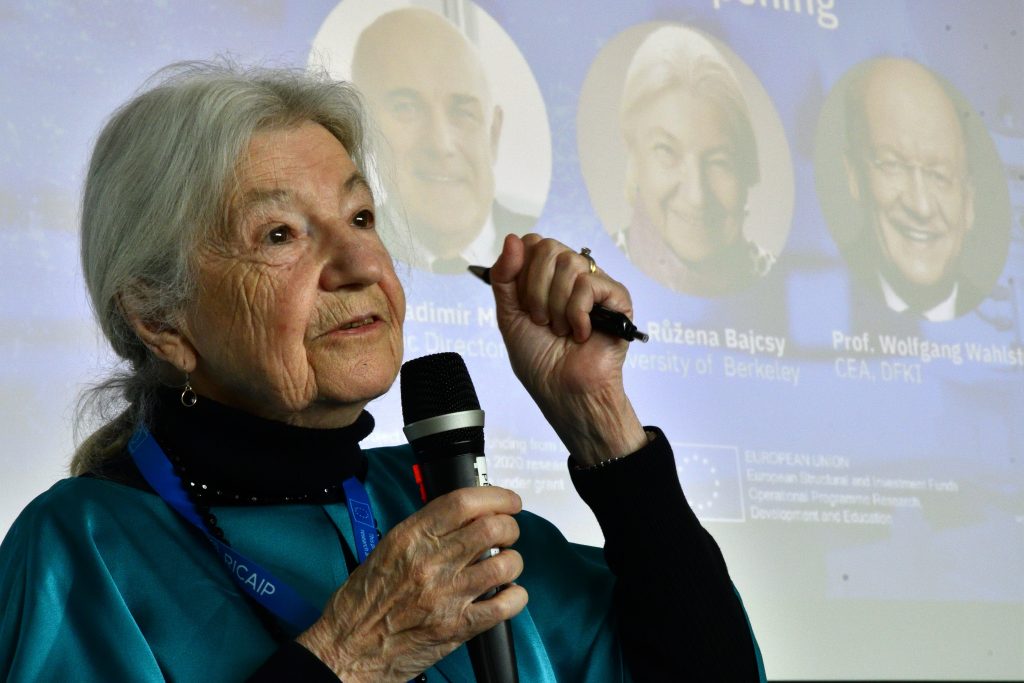
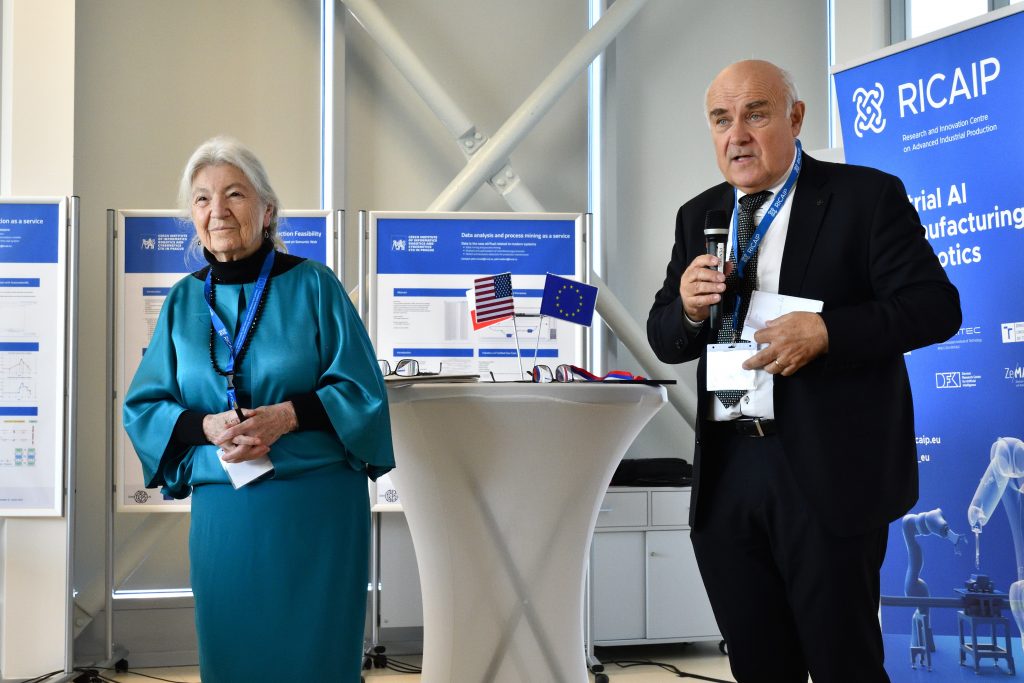
“The workshop was very timely since after one decade of Industrie 4.0 we had to identify the main challenges for the second decade of the fourth industrial revolution, which still has a long way to go. We identified the need for end-to-end manufacturing testbeds, which should support also distributed manufacturing as realized in cooperation with our Czech partners within the RICAIP Centre.”
Prof. Wolfgang Wahlster, DFKI
Another important topic for international cooperation is the standardisation and certification of hardware and software components as well as architectures and communication protocols for Industry 4.0 to ensure semantic interoperability. Standardisation and certification can be done only at the international level to prove that the systems work correctly. Security is very important too as manufacturing is on the top of the list of hacking and computer crime.
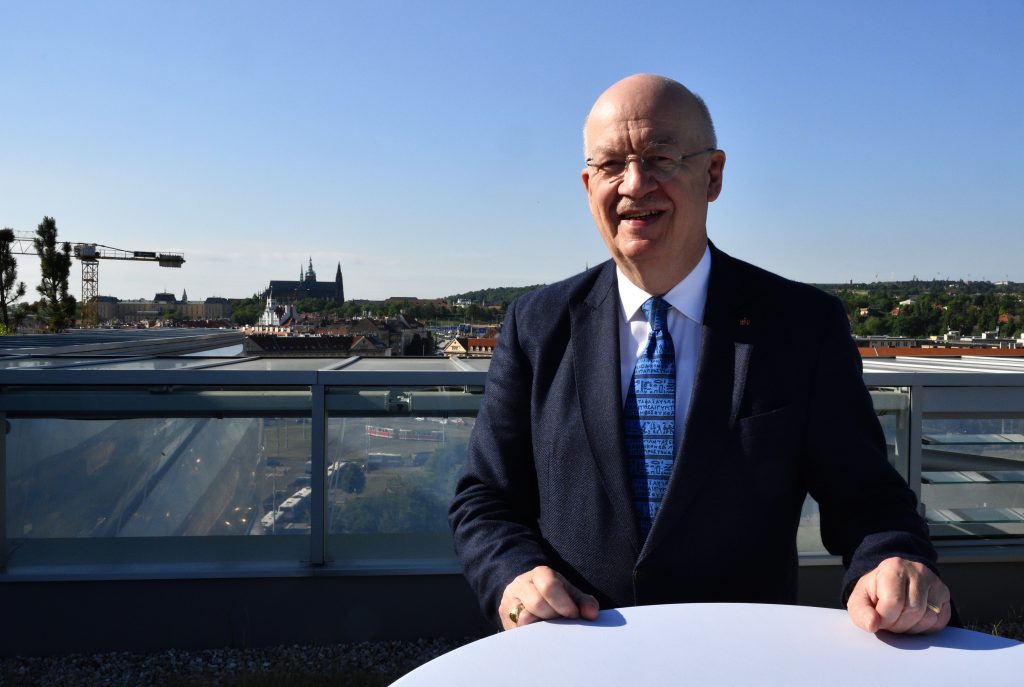
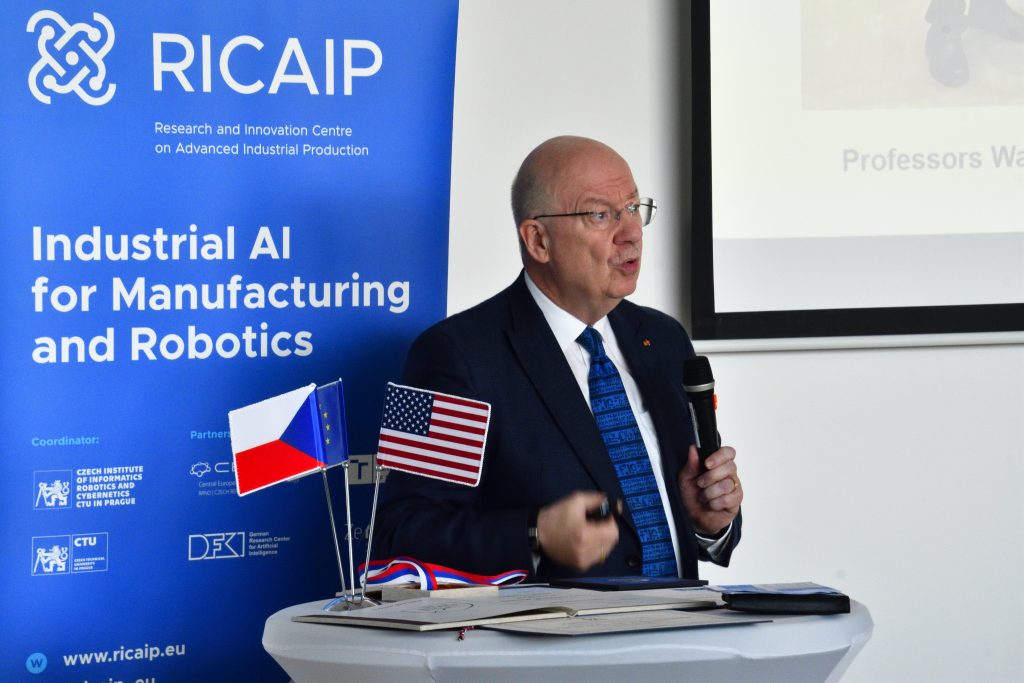
“In addition, we need comparison criteria and benchmarks for evaluating operating systems and software platforms for implementing smart factories in the Industry 4.0 paradigm, since it turned out that there are several competing approaches and the industry needs some guidance about which systems fulfil their needs best.
Prof. Wolfgang Wahlster, DFKI
Trends of industrial AI, 5G in the factory as well as edge, fog, cloud, and sky computing must be leveraged to strengthen the resilience of Industrie 4.0 solutions.“
The speakers mentioned several times that the most incremental progress has been made with the use of machine learning as the ability to do real-time object recognition on the shop floor. The combination of data-driven machine learning with engineering knowledge encoded in digital twins is another trend that has been identified in several talks. The innovators shall also focus more on remote maintenance and remote repair. This is a really important problem for industry and also in any emergency cases as shown during the covid situation, war, or natural disasters that create often also political pressures on supply chains.
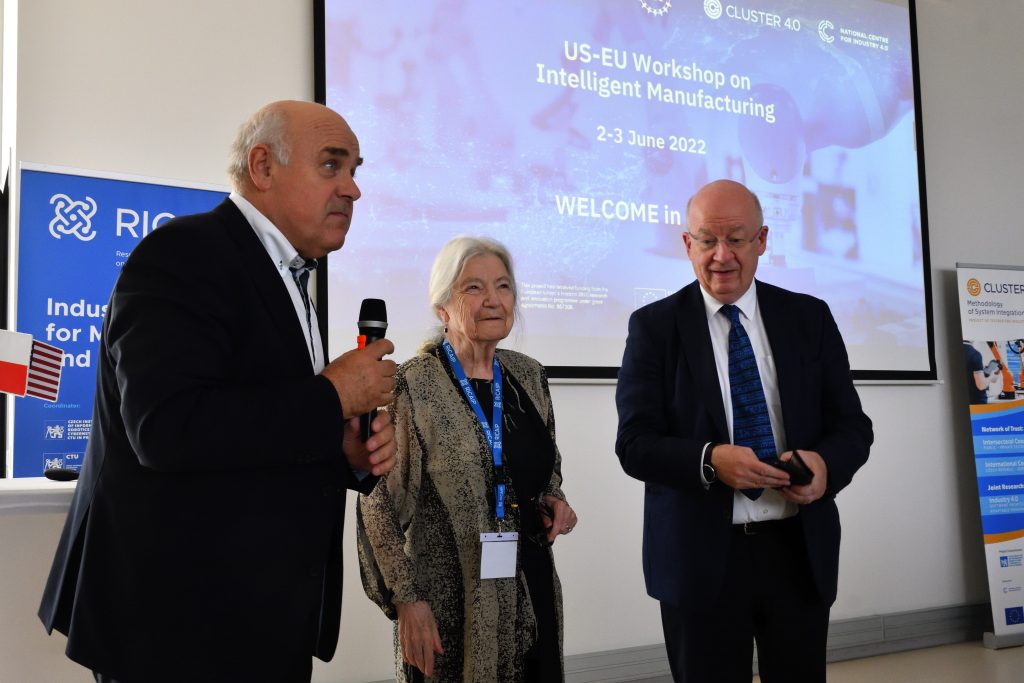
The discussions proved that new business models would be important for the further deployment of new approaches. From the simple purchase of a machine or licencing, the innovative business models are based on the performance or use of the machines.
“This is already done by some companies for example in Germany – you do not pay for a machine, but for the tasks that the machine performs, such as drilling a certain number of holes.”
Prof. Wolfgang Wahlster, DFKI – describes the already existing practice in some innovative enterprises.
The providers of the machines provide the full service of a machine, so the price is based on the effect that the machine is achieving. This requires completely new thinking of management in the spirit of business informatics.
Finally, hybrid teams of workers and collaborative robots with different skill sets will enable a new form of team robotics for complex manufacturing tasks. Hand in hand with this development, the collaborative robots go into a new dimension such as two-arm robots or mobile robots that are not fixed to one position for a worker. Team robotics with two or three robots working together with a team of humans is a very important trend that is enforced especially in automotive manufacturing.
Prof. Vladimír Mařík, scientific director at CIIRC CTU, referred that industry and intelligent manufacturing is a broad topic. This fact was also reflected in the selection of the speakers who came from California, Georgia, Illinois, and North Carolina as well as from European countries such as Germany, Slovakia or Spain.
“We are making research in some areas and also teams from for example the USA, Germany or Basque Country are doing similar research. Maybe we are talking with slightly different languages and use different approaches but machine learning, artificial intelligence, digital twins, sensing, operational systems for Industry 4.0, data services and data spaces remain in the focus of the entire community,” concludes this variety Prof. Mařík and continues: “We just opened the door for much wider cooperation with the use of the facilities that for example CIIRC CTU and DFKI can offer within the RICAIP Centre and that is open to any kind of international cooperation with the European and American universities and organisations.“
Prof. Vladimír Mařík, CIIRC CTU
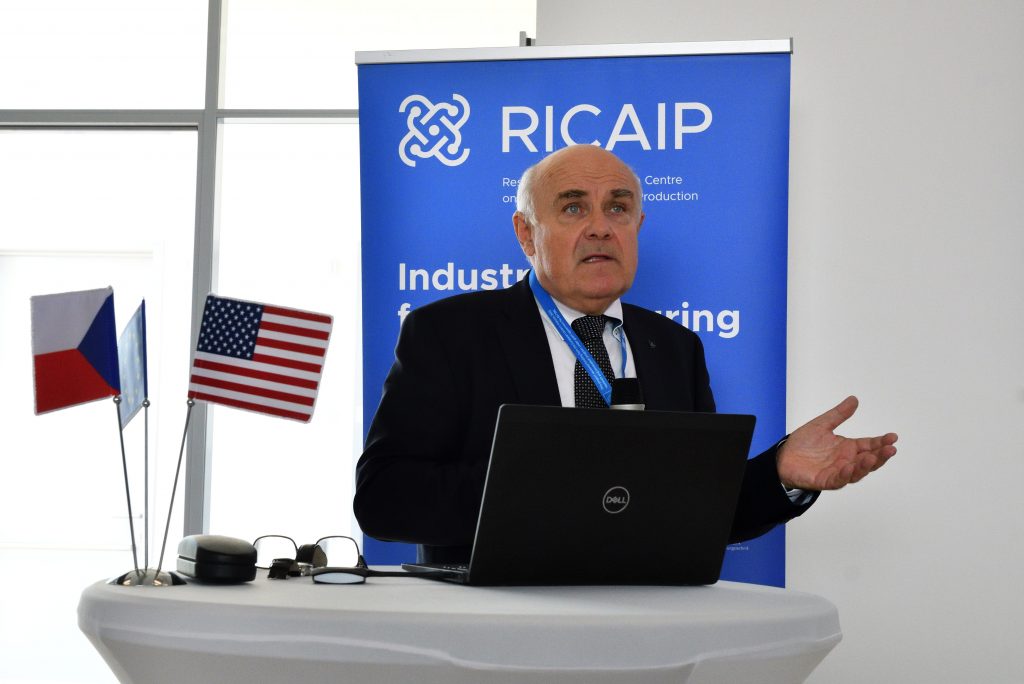
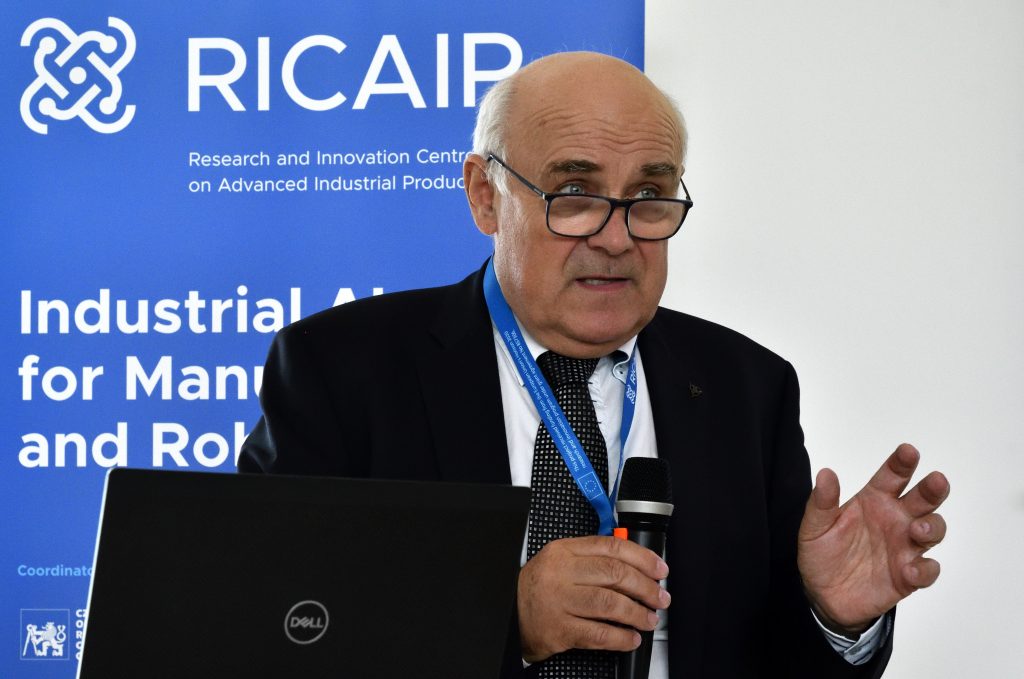
Prof. Wahlster added that the already existing collaborative distributed testbeds in the Czech Republic – in Prague, Brno and Ostrava – and Germany could now be extended with Spain and other European countries.
“It would be great to extend this collaboration also to the United States.”
Prof. Wolfgang Wahlster, DFKI
“Many American universities have a similar setup but many do not. The network of experimental manufacturing facilities is quite impressive and many US academic labs could be envious.”
Prof. Ruzena Bajcsy, UC Berkeley
From her point of view, this could be a motivation for a US-EU collaboration which could facilitate the US students to come to Prague and carry out some collaborative and yet exploration experiments in the context of the Industry 4.0 agenda.
“This approach to both parties could be a win-win and I hope to explore this approach shortly.”
Prof. Ruzena Bajcsy plans.
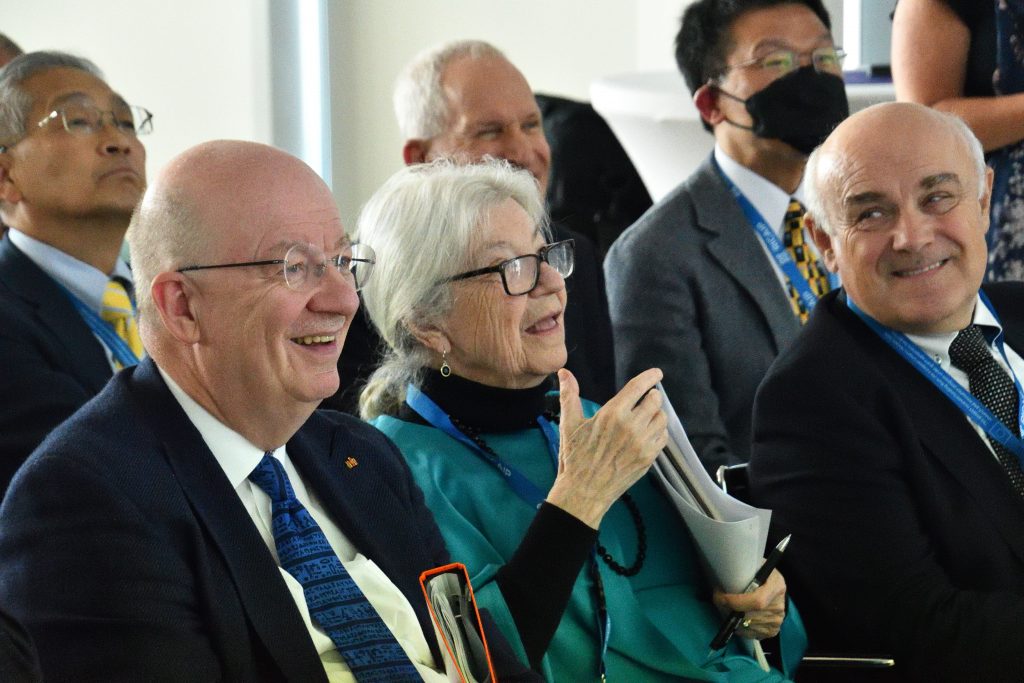
The first transatlantic workshop on AI in manufacturing was organised within the RICAIP Centre ecosystem: by CIIRC CTU, the National Centre for Industry 4.0 (NCI4.0) and DFKI, with the support of the National Science Foundation (NSF), an independent federal agency created by US Congress, and CLAIRE, the Confederation of Laboratories for Artificial Intelligence Research in Europe.